What is GMP Certificate and Why It Matters | Essential Guide
Discover why a GMP certificate is essential for manufacturing quality and compliance. Learn its impact on your business success. Read this article now!
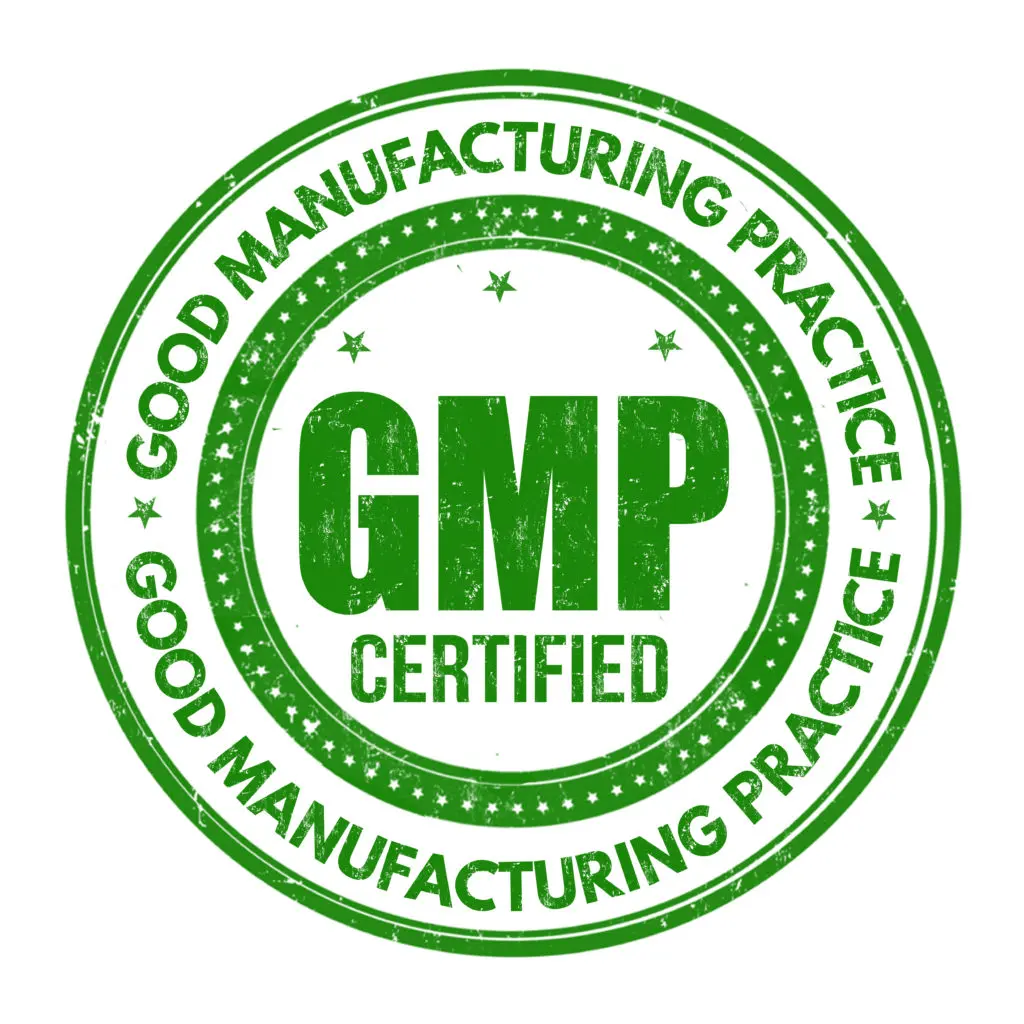
200+ buyers trust Torg for sourcing
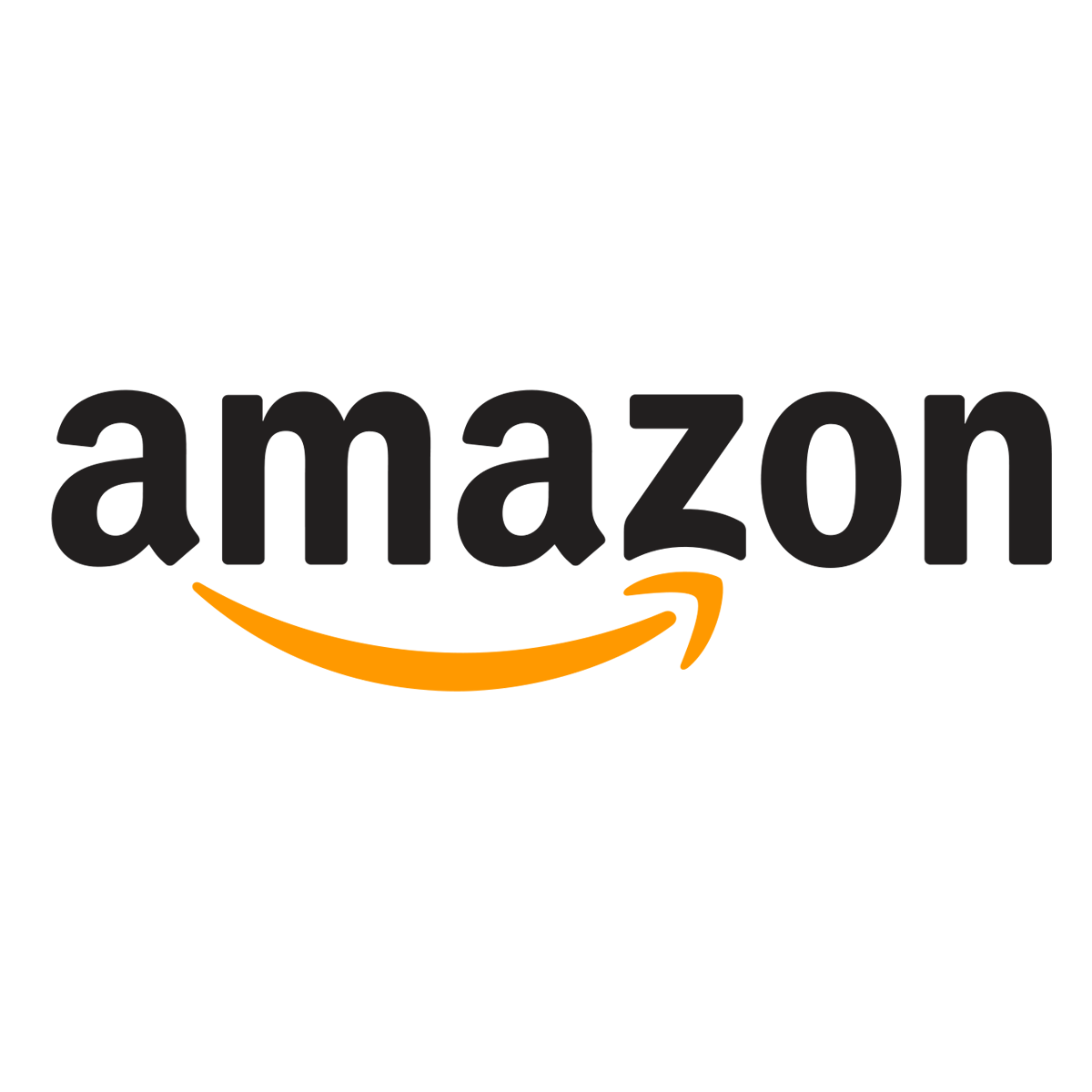
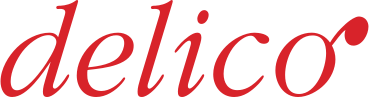
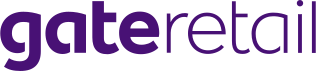
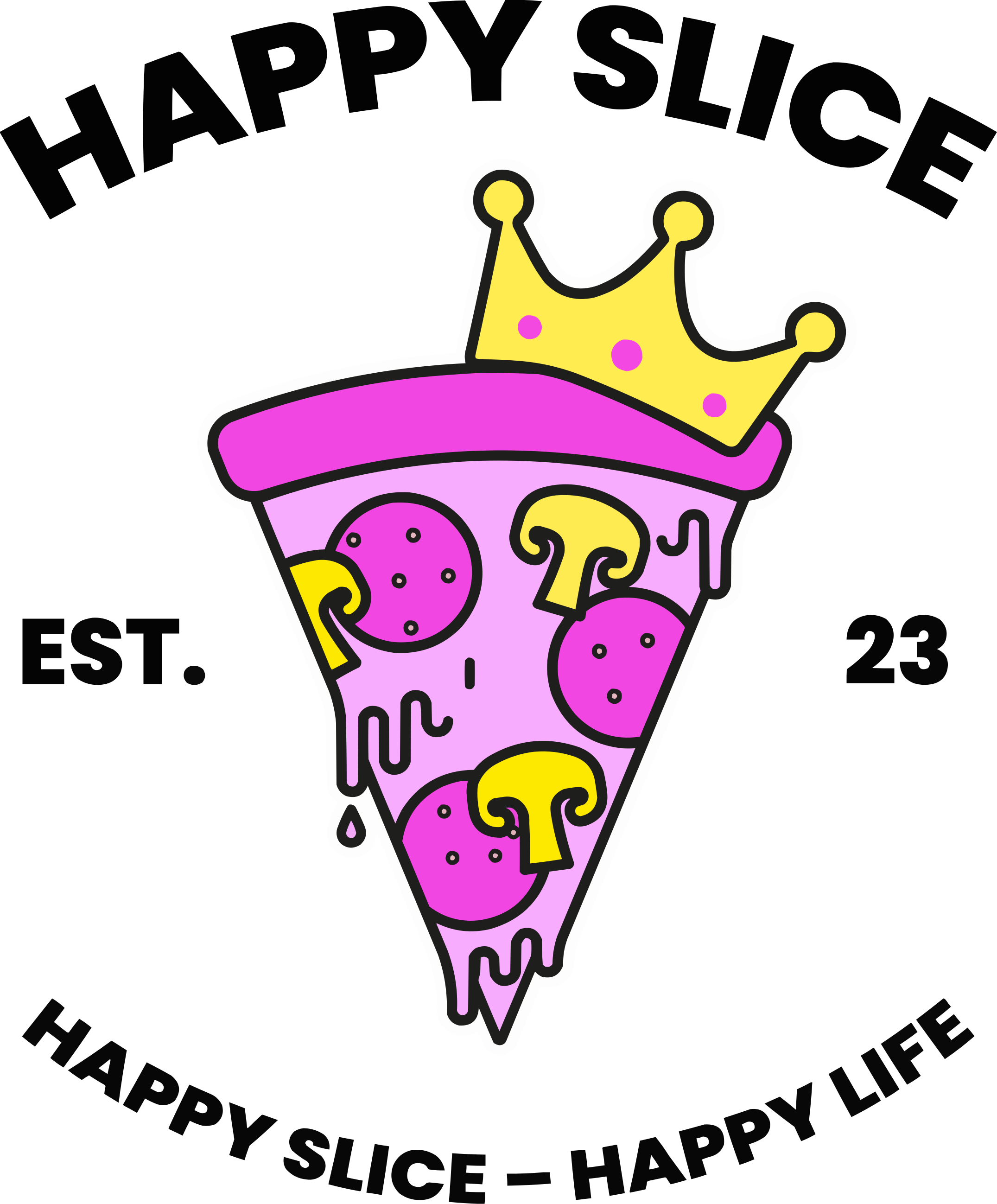
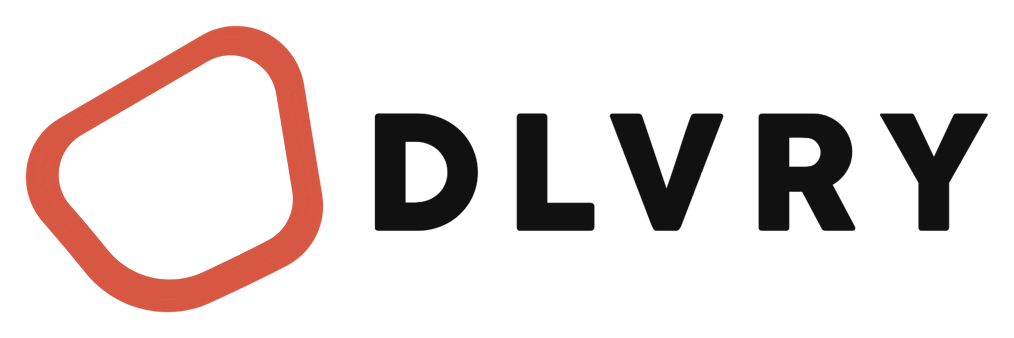
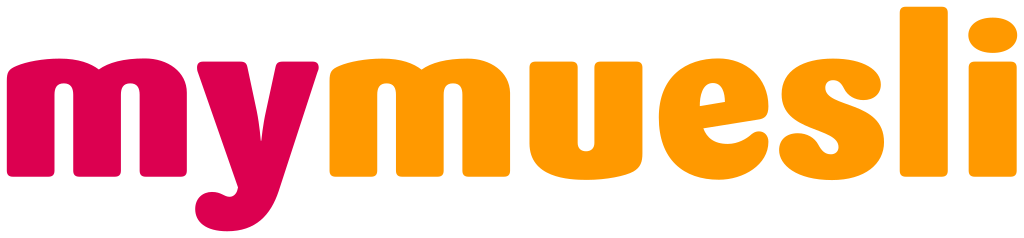
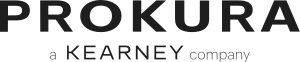
A GMP certificate is essential for manufacturers to ensure compliance with Good Manufacturing Practices (GMP)—a set of guidelines designed to uphold product quality, safety, and consistency. Industries such as pharmaceuticals, medical devices, cosmetics, and food production must follow these standards to meet regulatory requirements and protect consumers.
Regulatory bodies like the FDA and WHO enforce GMP certification to prevent contamination, errors, and safety risks. Without it, companies face product recalls, legal penalties, and loss of customer trust.
For manufacturers, getting a GMP certification not only strengthens credibility but also opens doors to global markets. This is why understanding its importance is key to maintaining compliance, ensuring quality, and staying competitive in the industry.
What is GMP Certificate?
A GMP Certificate stands for Good Manufacturing Practice Certificate. It is an official recognition or certification that a company or manufacturer adheres to the established quality standards for manufacturing products, especially in industries like pharmaceuticals, food, and cosmetics.
GMP guidelines ensure that products are consistently produced and controlled according to strict quality standards. These practices help minimize the risks involved in production that cannot be eliminated through testing the final product.
Importance of GMP Certification for Manufacturers
Obtaining a GMP certificate shows that a manufacturer follows these rigorous procedures and complies with the required standards for safety and quality. This is essential in industries where the products directly impact health, safety, and well-being, such as medicine, food, and cosmetics.
GMP guidelines serve as a set of guidelines for uniform manufacturing procedures, including the use of materials, equipment, and personnel hygiene. Compliance with these guidelines is usually required by regulatory bodies such as the FDA, which implements Current Good Manufacturing Practice (CGMP) regulations to ensure the identity, strength, quality, and purity of drug products.
Non-compliance, in turn, can result in serious penalties, such as product recall, lawsuits, and loss of business reputation. GMP certification is, hence, not merely a matter of regulation but a pledge towards quality control and to protect consumers.
Benefits of GMP Certification
Being "GMP-certified" isn't just for show. Here are some key advantages and benefits of having a GMP certification as a manufacturer:
Enhanced Product Quality and Safety
A GMP certified company ensures that their products meet strict quality standards, reducing risks of contamination, defects, and inconsistencies. Regulatory authorities like the FDA emphasize that CGMP regulations ensure proper monitoring and control of the manufacturing process, safeguarding consumer health (FDA, 2024).
Regulatory Compliance and Risk Mitigation
Being GMP certified demonstrates compliance with GMP regulations, helping manufacturers avoid legal issues, product recalls, and failed GMP inspections. Agencies like the European Medicines Agency (EMA) and national competent authorities require compliance for market approval and clinical trial authorization (FDA, 2024).
Increased Operational Efficiency
Compliance with GMP guidelines promotes standardization in manufacturing facility operations, minimizing wastage, errors, and expenditures. Effective procedures result in enhanced productivity and reduced production time, making firms competitive.
Market Access and Competitive Advantage
Numerous distributors and overseas markets necessitate GMP certification to attain high-quality products. The pharmaceutical industry and other regulated sectors gain higher credibility, worldwide market access, and consumer confidence.
Key GMP Requirements for Manufacturers
Following GMP guidelines is essential for ensuring product quality, safety, and regulatory compliance. Here are the key GMP requirements:
1. Quality Management System (QMS)
They need a Quality Management System (QMS) for the assurance of quality control consistently and adherence to the rules of GMP. This involves documented procedure, audit, and ongoing improvement to adhere to high-quality standards (FDA, 2024).
2. Trained and Hygienic Staff
All staff needs to be trained on GMP principles and practice strict hygiene procedures to avoid contamination. This means that protective clothing, cleanliness, and following safety procedures should be practiced at all times (ISPE, 2024).
3. Correct Facility and Equipment
The equipment and the manufacturing facility need to be clean, properly maintained, and contamination-proof. Maintenance of equipment on a regular basis, calibration, and validation help ensure that the manufacturing process is controlled (EMA, 2024).
4. Proper Documentation
Producers need to maintain precise records for each stage of the production process, from raw materials to finished product. Accurate documentation makes GMP inspections run smoothly and facilitates tracing problems in case there are issues (Health Canada, 2024).
5. Process and Production Controls
Establishing well-defined production and process controls is essential to ensure that products are consistently manufactured to meet quality specifications. This includes validating critical processes, monitoring in-process parameters, and implementing controls to prevent deviations. (FDA, 2024).
6. Quality Control and Testing
A GMP-certified manufacturer should have a quality control department to analyze raw materials and finished goods. Also, periodic GMP inspections guarantee adherence to the certification standards. The FDA notes that CGMP regulations ensure proper design, monitoring, and control of manufacturing processes and facilities. This applies to all, most especially in the pharmaceutical industry (FDA, 2024).
7. Safe Handling of Materials
Raw materials, parts, and finished goods need to be appropriately labeled, warehoused, and shipped so as not to confuse or contaminate each other. Precise handling processes ensure product integrity (WHO, 2024).
8. Complaint Handling and Recalls
Manufacturers need to have a mechanism for tracking customer complaints and recalling faulty products when required. Adequate investigation and corrective measures ensure GMP compliance and consumer protection (ISPE, 2024).
GMP Certification Process: Step-by-Step Guide
A single lapse in manufacturing quality can lead to costly recalls, legal issues, or even risks to consumer safety. GMP certification helps prevent these problems by ensuring consistent quality and compliance across industries such as food production, cosmetics, medical devices, and pharmaceutical manufacturers. Here’s a step-by-step guide to the certification process:
Understand GMP Requirements
Start by getting a clear idea of Good Manufacturing Practice (GMP) rules that apply to your business. These regulations, mandated by national competent authorities, delineate the required practices for ensuring product quality and safety. The U.S. Food and Drug Administration (FDA) offers extensive resources regarding CGMP requirements.
Prepare for Certification
Before applying, companies should conduct a self-assessment to identify gaps in their manufacturing processes. This includes staff training, documentation updates, and adherence to protocols necessary for clinical trial authorisation and GDP inspections. Aligning with GMP guidelines early helps avoid compliance issues later (FDA, 2024)
Choose Certifying Authority
Choose a suitable certifying authority accepted by regulatory authorities. In the European Union, the national competent authorities issue GMP certification after inspections. In fact, the EU has MRAs on GMP with EU member states like Australia, Canada, Israel, Japan, New Zealand, Switzerland and the United States. All these agreements cover human/veterinary medicines; however the detailed product scope varies.
Submit Application and Documentation
Manufacturers must compile detailed records of their manufacturing processes, including quality control measures and supply chain transparency for active substances, especially in pharmaceutical products. Submission must meet the standards set by regulatory bodies for approval (WHO, 2024).
On-Site Inspection and Audit
The certifying body will carry out an on-site inspection to ensure compliance with GMP regulations. The audit entails assessing facilities, equipment, personnel practices, and quality control systems. All aspects of production must comply with GMP standards for certification approval.
Certification Decision
After evaluating inspection reports, the certifying authority decides whether to grant GMP certification. Compliance with GMP guidelines ensures manufacturers meet the highest industry standards for biological medicinal products and active substances (FDA, 2024).
Maintain Compliance
Once GMP certified, companies must continuously follow GMP regulations and prepare for routine GDP inspections. Staying compliant with CGMP requirements helps businesses maintain their certification and meet evolving regulatory expectations (WHO, 2024).
Common Challenges in Obtaining GMP Certification
A process is not a process without its own set of roadblocks. These are the common challenges in obtaining GMP certification:
- High Implementation Costs: Establishing GMP-compliant systems requires significant financial investment in quality management systems, facility upgrades, and comprehensive staff training. These expenses can be substantial, especially for small to medium-sized enterprises.
- Complex Regulatory Requirements: Navigating the intricate and detailed guidelines set forth by various competent authorities demands a thorough understanding of detailed GMP requirements. Non-compliance can lead to regulatory actions, including fines or suspension of manufacturing licenses.
- Global Standard Variations: Differences in GMP standards across regions necessitate that manufacturers tailor their processes to meet the legal basis and intended use criteria of each market, adding complexity to the certification process.
Cost of GMP Certification
The cost of GMP (Good Manufacturing Practice) certification can vary significantly based on several factors, including:
Generally, GMP certification costs can range from:
For food and beverage GMP certification in Europe, you can expect an overall initial investment ranging from €7,000 to €40,000 for small to large businesses, factoring in audit costs, preparation, and consulting. Ongoing costs for maintenance and re-certification would typically range from €3,000 to €10,000 annually.
- Size and Complexity of the Business: Larger or more complex manufacturing operations often incur higher certification costs due to the number of processes involved.
- Location: Certification fees can differ by country or region due to local regulations and the certifying bodies' rates.
- Consulting and Preparation Costs: Many companies hire external consultants to help prepare for the certification, which adds to the cost. This can range from a few thousand to tens of thousands of dollars.
- Certifying Body: Different certifying organizations may charge varying rates. Some of the well-known bodies include the FDA (in the U.S.), ISO (International Organization for Standardization), or other national/regional regulatory authorities.
- Scope of the Certification: Whether you are certifying a single product line or multiple facilities may influence the cost.
- Small businesses: $5,000 to $20,000 USD
- Medium businesses: $20,000 to $50,000 USD
- Large enterprises: $50,000 to $100,000+ USD
Global GMP Certification Standards: Key Differences
Standards of GMP differ between regions, and one can note clear differences in, for example, regulatory bodies such as the United States' Food and Drug Administration (FDA) and the European Medicines Agency (EMA). For example, the EMA has greater requirement on record-keeping and documentation, setting concise guidelines on designing standard operating procedure and batch documentation. An appreciation of the dissimilarities can be necessary in order for companies to achieve more than one's GMP certifications.
Conclusion
Take the example of Chi Pharmaceuticals Limited, a Nigerian pharmaceuticals manufacturer that was having trouble complying with certain GMP requirements because of excessive expenses and intricate detailed guidelines. The firm initially experienced setbacks, such as warnings from a competent authority for non-compliance with GMP rules.
But after investing in facility improvements, employee training, and improved quality control systems, they were able to achieve GMP certification. This accomplishment enabled them to broaden their marketability, enhance the credibility of their products, and adhere to the regulatory measures initiated by the European Commission and other international agencies.
Their experience shows that although gaining GMP certification can be challenging, it ultimately enhances safety for medicinal products, maintains active pharmaceutical ingredients consistency, and reveals business prospects to the international market.
Frequently Asked Questions
What is a GMP certificate?
A GMP (Good Manufacturing Practice) certificate ensures that a company adheres to quality standards in production, ensuring safety, consistency, and quality of products. It is awarded after an audit by an accredited body, confirming that manufacturing processes comply with regulatory and safety guidelines.
Who needs GMP certification?
GMP certification is required for businesses involved in the production of products where quality, safety, and consistency are critical. This includes industries like pharmaceuticals, food and beverages, cosmetics, medical devices, and dietary supplements. It ensures compliance with regulatory standards and consumer safety.
Can an individual become GMP certified?
Individuals cannot be GMP certified, but they can complete GMP training to understand specific guidelines and enhance compliance skills within a manufacturing facility.
How to get GMP certificate?
Companies must meet specific GMP requirements, apply to a competent authority, undergo audits, pass GMP inspections, and maintain compliance to receive and retain certification.