What are the GMP Guidelines?
Good Manufacturing Practice (GMP) is a critical aspect of quality assurance in manufacturing, especially in industries like food production, pharmaceuticals, and cosmetics. But what are GMP guidelines? This guide provides an in-depth look at GMP, its components, principles, regulations, and the importance of compliance for maintaining product safety and quality.
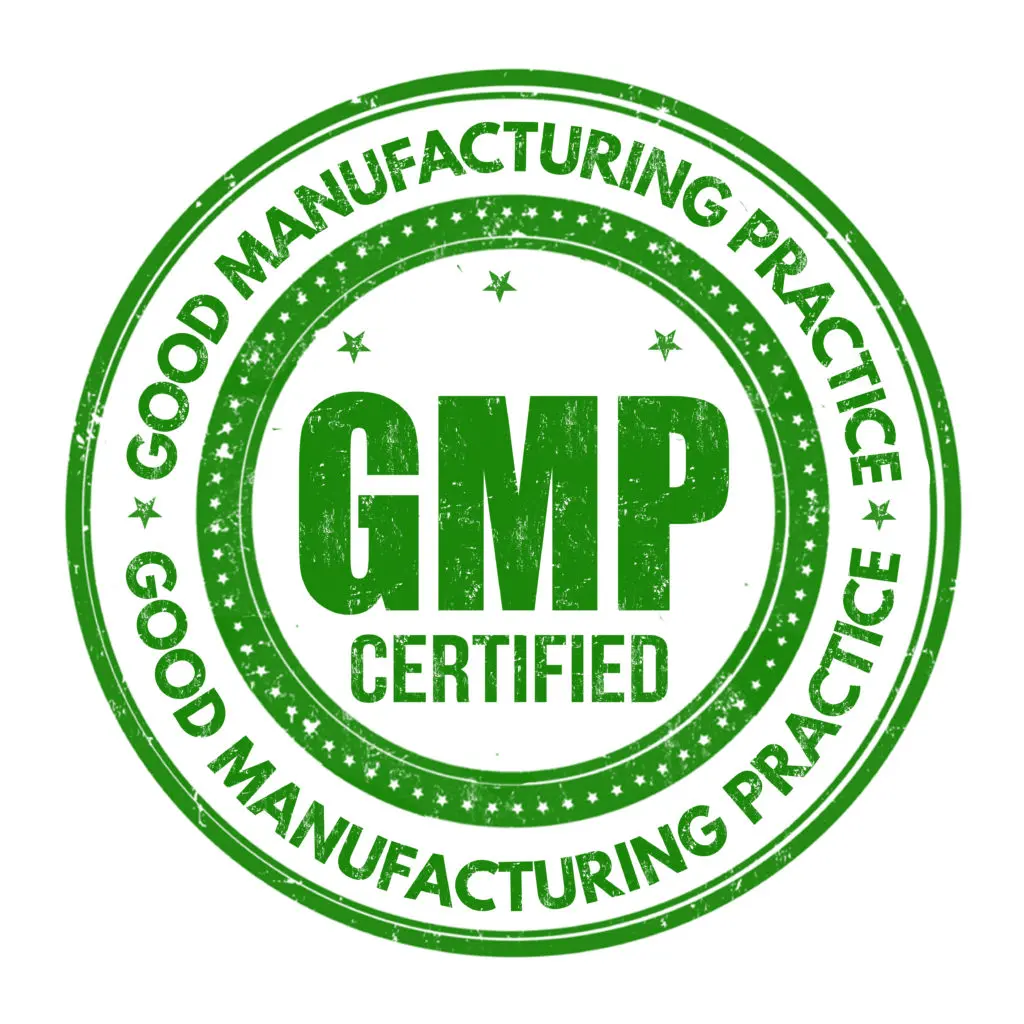
200+ buyers trust Torg for sourcing
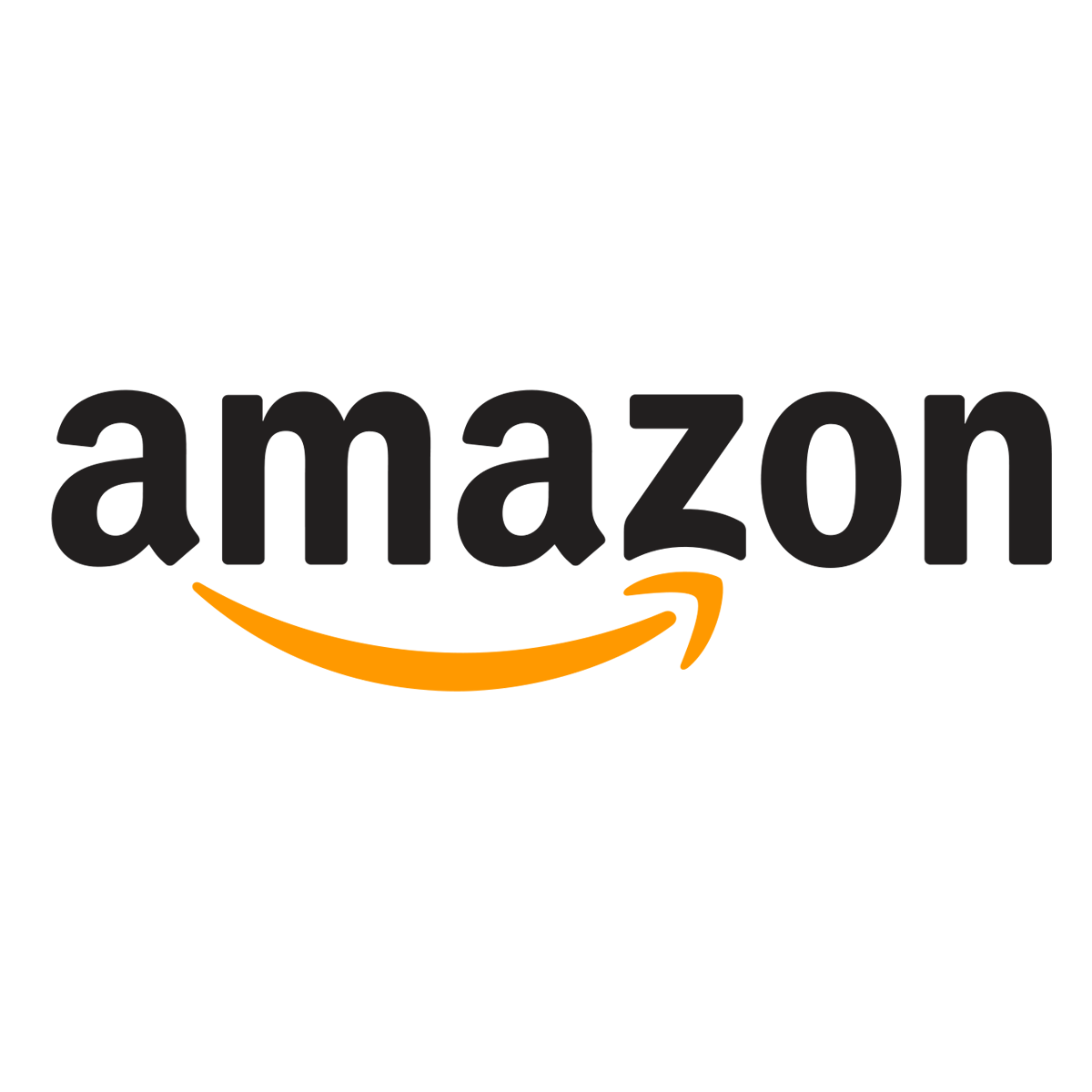
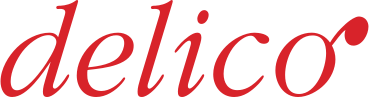
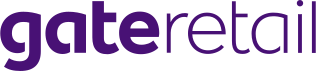
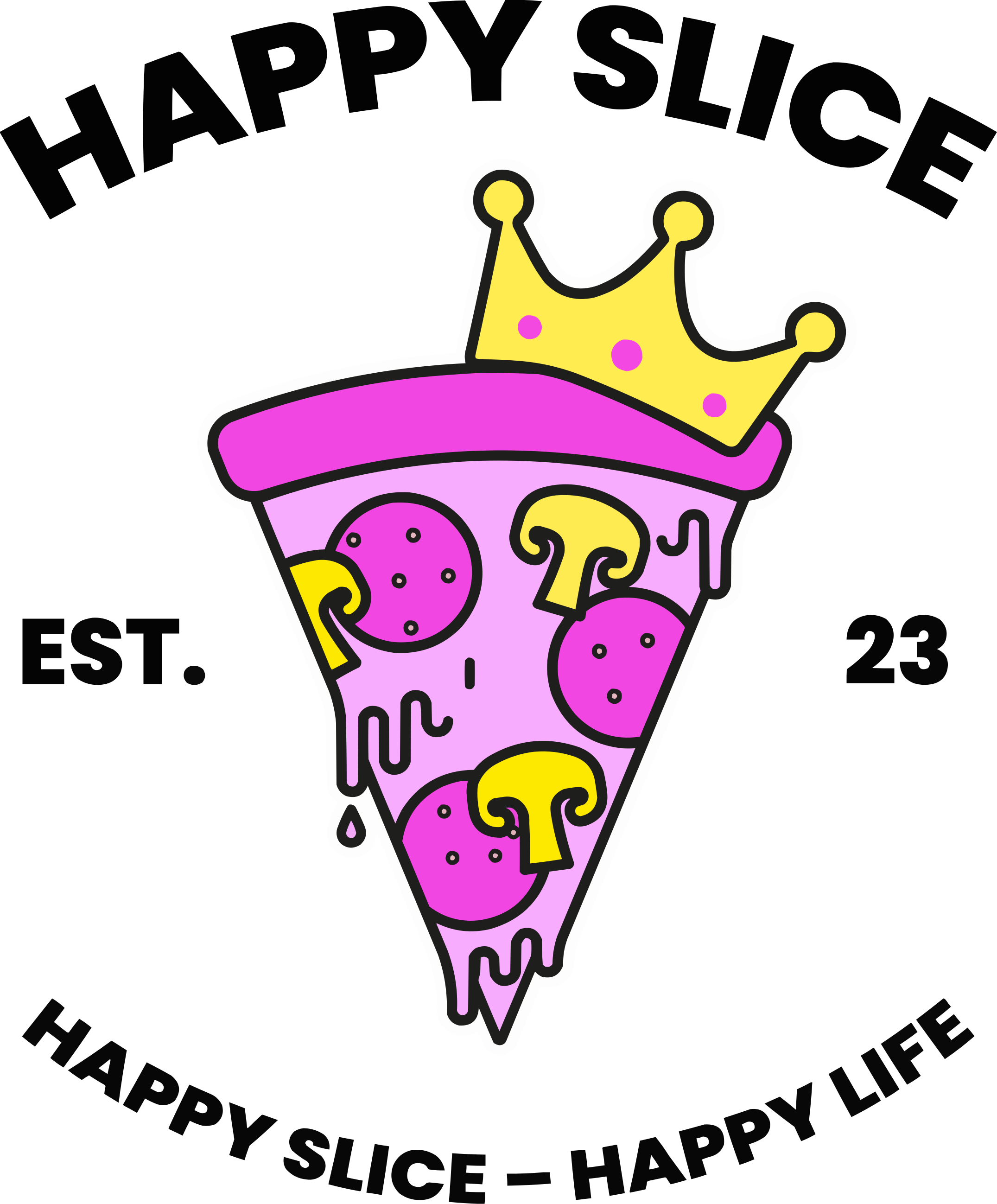
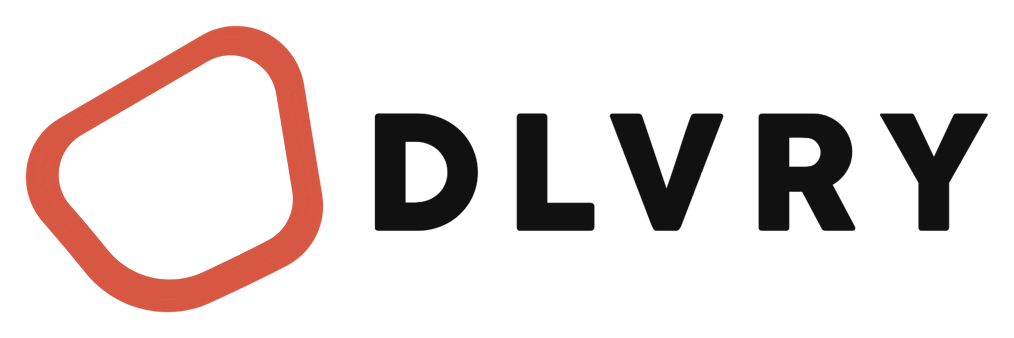
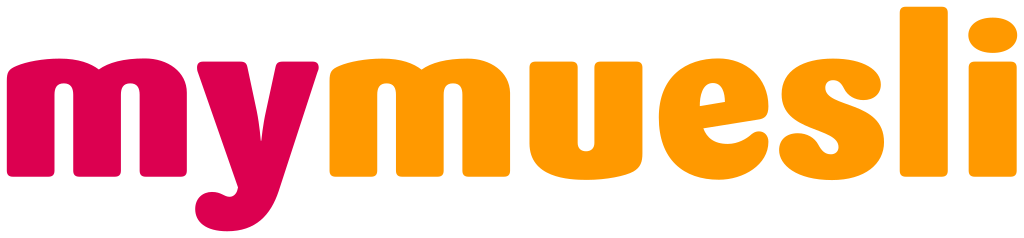
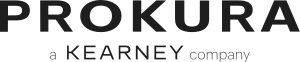
What is GMP?
GMP, or Good Manufacturing Practice, represents a system of guidelines and regulations that are crucial for ensuring that products meet specified quality standards throughout their production. GMP aims to minimize risks associated with food preparation, and cosmetic manufacturing by promoting consistency, safety, and effectiveness.
The core of GMP is the systematic approach to manufacturing that includes comprehensive quality control, thorough documentation, and well-defined procedures. These practices are designed to ensure that every product meets the required standards and is free from contamination or defects.
Know more about GMP Certification
The core of GMP is the systematic approach to manufacturing that includes comprehensive quality control, thorough documentation, and well-defined procedures. These practices are designed to ensure that every product meets the required standards and is free from contamination or defects.
Know more about GMP Certification
What Are The Main Components of GMP?
To effectively implement GMP guidelines, it is essential to understand the main components that contribute to a successful quality management system:
The role of personnel in GMP is vital. Employees must be adequately trained and qualified to perform their tasks competently. This includes not only the initial training but also ongoing education to keep up with new regulations and best practices. Proper training ensures that employees understand their responsibilities and the importance of their role in maintaining GMP standards.
GMP guidelines stipulate that facilities and equipment must be suitable for their intended purpose. This means maintaining a clean and organized environment that prevents contamination. Equipment must be regularly calibrated and maintained to ensure its proper functioning. By adhering to these requirements, manufacturers can avoid potential issues that could affect the quality of their products.
Documentation is a cornerstone of GMP. It involves creating and maintaining detailed records of all manufacturing processes, quality control measures, and deviations from standard procedures. This documentation not only provides a clear record of what has been done but also helps in tracing any issues that may arise.
The production process must follow standardized procedures to ensure consistency and quality. This includes everything from raw material handling to the final product. GMP guidelines require that production processes are well-defined, monitored, and controlled to prevent any deviations that could affect product quality.
Quality control is a critical aspect of GMP. It involves testing and validating products to ensure they meet the specified quality standards. This includes conducting routine inspections, performing analytical tests, and validating processes.
Personnel
The role of personnel in GMP is vital. Employees must be adequately trained and qualified to perform their tasks competently. This includes not only the initial training but also ongoing education to keep up with new regulations and best practices. Proper training ensures that employees understand their responsibilities and the importance of their role in maintaining GMP standards.
Facilities and Equipment
GMP guidelines stipulate that facilities and equipment must be suitable for their intended purpose. This means maintaining a clean and organized environment that prevents contamination. Equipment must be regularly calibrated and maintained to ensure its proper functioning. By adhering to these requirements, manufacturers can avoid potential issues that could affect the quality of their products.
Documentation
Documentation is a cornerstone of GMP. It involves creating and maintaining detailed records of all manufacturing processes, quality control measures, and deviations from standard procedures. This documentation not only provides a clear record of what has been done but also helps in tracing any issues that may arise.
Production
The production process must follow standardized procedures to ensure consistency and quality. This includes everything from raw material handling to the final product. GMP guidelines require that production processes are well-defined, monitored, and controlled to prevent any deviations that could affect product quality.
Quality Control
Quality control is a critical aspect of GMP. It involves testing and validating products to ensure they meet the specified quality standards. This includes conducting routine inspections, performing analytical tests, and validating processes.
What are the Main Principles of GMP?
The GMP guidelines are based on several fundamental principles that guide their implementation:
Quality assurance is a primary principle of GMP. It involves implementing a comprehensive system that ensures every aspect of production meets quality standards from the outset. This principle emphasizes the importance of preventing defects rather than simply detecting them after they occur.
Consistency is crucial in GMP. It ensures that products are produced in a uniform manner, maintaining the same quality and effectiveness in every batch. Consistency helps build consumer trust and ensures that products perform as expected.
GMP guidelines stress the importance of traceability. This means documenting every step of the production process to track and address any issues that may arise. Traceability allows manufacturers to quickly identify and resolve problems, ensuring that products remain safe and effective.
Compliance with regulatory requirements is essential for GMP. Manufacturers must adhere to the specific regulations set forth by governing bodies to maintain product integrity and safety. Compliance ensures that products meet all necessary standards and avoid legal issues.
Quality Assurance
Quality assurance is a primary principle of GMP. It involves implementing a comprehensive system that ensures every aspect of production meets quality standards from the outset. This principle emphasizes the importance of preventing defects rather than simply detecting them after they occur.
Consistency
Consistency is crucial in GMP. It ensures that products are produced in a uniform manner, maintaining the same quality and effectiveness in every batch. Consistency helps build consumer trust and ensures that products perform as expected.
Traceability
GMP guidelines stress the importance of traceability. This means documenting every step of the production process to track and address any issues that may arise. Traceability allows manufacturers to quickly identify and resolve problems, ensuring that products remain safe and effective.
Compliance
Compliance with regulatory requirements is essential for GMP. Manufacturers must adhere to the specific regulations set forth by governing bodies to maintain product integrity and safety. Compliance ensures that products meet all necessary standards and avoid legal issues.
What are the GMP Regulations?
These regulations ensure that manufacturers comply with the necessary guidelines to produce safe and effective products. Some key GMP regulations include:
In the United States, the Food and Drug Administration (FDA) enforces GMP standards for food products, and certain medical devices. The FDA’s regulations focus on ensuring that products are consistently manufactured and meet safety and quality standards.
The World Health Organization (WHO) sets GMP standards for global practices, particularly in low and middle-income countries. WHO’s guidelines aim to improve the quality and safety of pharmaceutical products worldwide, ensuring that they meet international standards.
FDA Regulations (USA)
In the United States, the Food and Drug Administration (FDA) enforces GMP standards for food products, and certain medical devices. The FDA’s regulations focus on ensuring that products are consistently manufactured and meet safety and quality standards.
WHO GMP Guidelines
The World Health Organization (WHO) sets GMP standards for global practices, particularly in low and middle-income countries. WHO’s guidelines aim to improve the quality and safety of pharmaceutical products worldwide, ensuring that they meet international standards.
How to Comply with GMP Guidelines?
Complying with GMP guidelines involves several critical steps.
Creating a comprehensive GMP compliance plan is essential for meeting quality standards. This plan should outline how your organization will achieve GMP compliance, including the development of standard operating procedures (SOPs), training programs, and quality control measures. A well-defined plan ensures that all aspects of manufacturing are covered and helps maintain consistency.
Training is a fundamental aspect of GMP compliance. Ensure that all employees are knowledgeable about GMP requirements and their role in maintaining compliance. Regular training sessions should be conducted to keep staff updated on any changes in regulations or best practices. Well-trained personnel are crucial for implementing GMP standards effectively.
This includes standard operating procedures, batch records, quality control records, and training records. Proper documentation provides transparency and traceability, allowing manufacturers to demonstrate compliance during inspections and audits.
Conducting internal audits and preparing for external inspections are crucial for maintaining GMP compliance. Regular audits help identify any issues or deficiencies in the manufacturing process, allowing for prompt corrective actions. External inspections by regulatory bodies ensure that manufacturers adhere to GMP regulations and maintain high-quality standards.
Regularly review and update procedures, training programs, and equipment to ensure that practices remain effective and up-to-date. Manufacturers can improve product quality and maintain GMP compliance by adopting a continuous improvement culture.
Develop a GMP Compliance Plan
Creating a comprehensive GMP compliance plan is essential for meeting quality standards. This plan should outline how your organization will achieve GMP compliance, including the development of standard operating procedures (SOPs), training programs, and quality control measures. A well-defined plan ensures that all aspects of manufacturing are covered and helps maintain consistency.
Train Personnel
Training is a fundamental aspect of GMP compliance. Ensure that all employees are knowledgeable about GMP requirements and their role in maintaining compliance. Regular training sessions should be conducted to keep staff updated on any changes in regulations or best practices. Well-trained personnel are crucial for implementing GMP standards effectively.
Implement Proper Documentation
This includes standard operating procedures, batch records, quality control records, and training records. Proper documentation provides transparency and traceability, allowing manufacturers to demonstrate compliance during inspections and audits.
Regular Audits and Inspections
Conducting internal audits and preparing for external inspections are crucial for maintaining GMP compliance. Regular audits help identify any issues or deficiencies in the manufacturing process, allowing for prompt corrective actions. External inspections by regulatory bodies ensure that manufacturers adhere to GMP regulations and maintain high-quality standards.
Continuous Improvement
Regularly review and update procedures, training programs, and equipment to ensure that practices remain effective and up-to-date. Manufacturers can improve product quality and maintain GMP compliance by adopting a continuous improvement culture.
What is GMP-compliant Documentation?
GMP-compliant documentation is crucial for ensuring transparency and traceability throughout the manufacturing process. It includes various types of records that demonstrate adherence to GMP standards:
SOPs provide detailed instructions on how to perform specific tasks to ensure consistency and quality. These procedures cover all aspects of manufacturing, from raw material handling to final product testing. SOPs are essential for maintaining standardized practices and ensuring that every step of the production process meets GMP requirements.
Batch records document the details of each batch of products produced. This includes information on ingredients, production processes, quality control results, and any deviations from standard procedures. Batch records provide a comprehensive overview of the production process and help trace any issues that may arise.
Quality control records document the results of tests and inspections performed to verify that products meet specified quality standards. These records include data on product testing, equipment calibration, and any corrective actions taken. Quality control records are crucial for ensuring that products are safe and effective.
Training records document the training sessions and certifications for personnel. These records help ensure that employees are qualified and knowledgeable about GMP requirements. Training records also demonstrate that employees have received the necessary education to perform their tasks effectively.
Standard Operating Procedures (SOPs)
SOPs provide detailed instructions on how to perform specific tasks to ensure consistency and quality. These procedures cover all aspects of manufacturing, from raw material handling to final product testing. SOPs are essential for maintaining standardized practices and ensuring that every step of the production process meets GMP requirements.
Batch Records
Batch records document the details of each batch of products produced. This includes information on ingredients, production processes, quality control results, and any deviations from standard procedures. Batch records provide a comprehensive overview of the production process and help trace any issues that may arise.
Quality Control Records
Quality control records document the results of tests and inspections performed to verify that products meet specified quality standards. These records include data on product testing, equipment calibration, and any corrective actions taken. Quality control records are crucial for ensuring that products are safe and effective.
Training Records
Training records document the training sessions and certifications for personnel. These records help ensure that employees are qualified and knowledgeable about GMP requirements. Training records also demonstrate that employees have received the necessary education to perform their tasks effectively.
Why is GMP Important for Manufacturing?
Adhering to GMP guidelines is essential for several reasons:
One of the primary reasons for following GMP guidelines is to ensure product safety. GMP practices help prevent contamination, cross-contamination, and other hazards that could compromise the safety of products. By maintaining clean facilities, using appropriate equipment, and implementing rigorous quality control measures, manufacturers can ensure that their products are safe for consumers.
Consistency in product quality is another critical aspect of GMP. By adhering to standardized procedures and maintaining strict quality control measures, manufacturers can produce products that meet specified quality standards. Consistent product quality helps build consumer trust and ensures that products perform as expected.
GMP regulations play a vital role in protecting consumer health. By ensuring that products are manufactured to high standards, GMP helps reduce the risk of adverse effects and ensures that consumers receive safe and effective products. Compliance with GMP guidelines contributes to the overall health and well-being of consumers.
Ensuring Product Safety
One of the primary reasons for following GMP guidelines is to ensure product safety. GMP practices help prevent contamination, cross-contamination, and other hazards that could compromise the safety of products. By maintaining clean facilities, using appropriate equipment, and implementing rigorous quality control measures, manufacturers can ensure that their products are safe for consumers.
Maintaining Product Quality
Consistency in product quality is another critical aspect of GMP. By adhering to standardized procedures and maintaining strict quality control measures, manufacturers can produce products that meet specified quality standards. Consistent product quality helps build consumer trust and ensures that products perform as expected.
Protecting Consumer Health
GMP regulations play a vital role in protecting consumer health. By ensuring that products are manufactured to high standards, GMP helps reduce the risk of adverse effects and ensures that consumers receive safe and effective products. Compliance with GMP guidelines contributes to the overall health and well-being of consumers.
Conclusion
GMP Guidelines are a comprehensive set of principles and regulations designed to ensure that products are manufactured to the highest standards of quality and safety. From understanding the core components and principles of GMP to complying with regulations and maintaining proper documentation, adhering to GMP is essential for any manufacturer aiming to produce safe and reliable products. By following these guidelines, manufacturers can protect consumer health, maintain product quality, and ensure overall safety in their operations. Compliance with GMP is not just a regulatory requirement but a commitment to excellence in manufacturing practices.