cGMP Certification: Meaning, Requirements & More
Ensure your product quality and regulatory compliance with cGMP certification. Learn its benefits, requirements, and steps to achieve this certification.
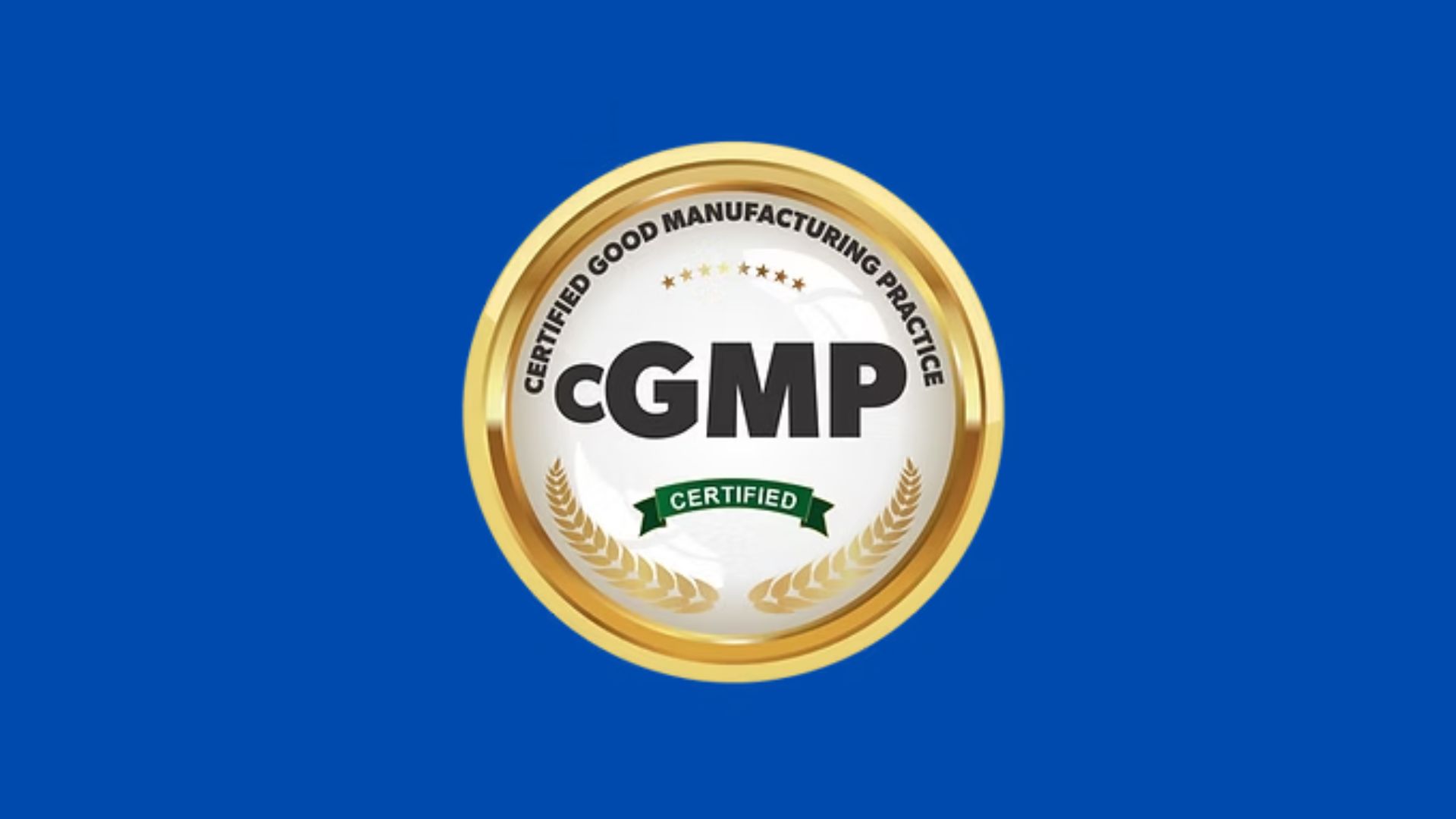
200+ buyers trust Torg for sourcing
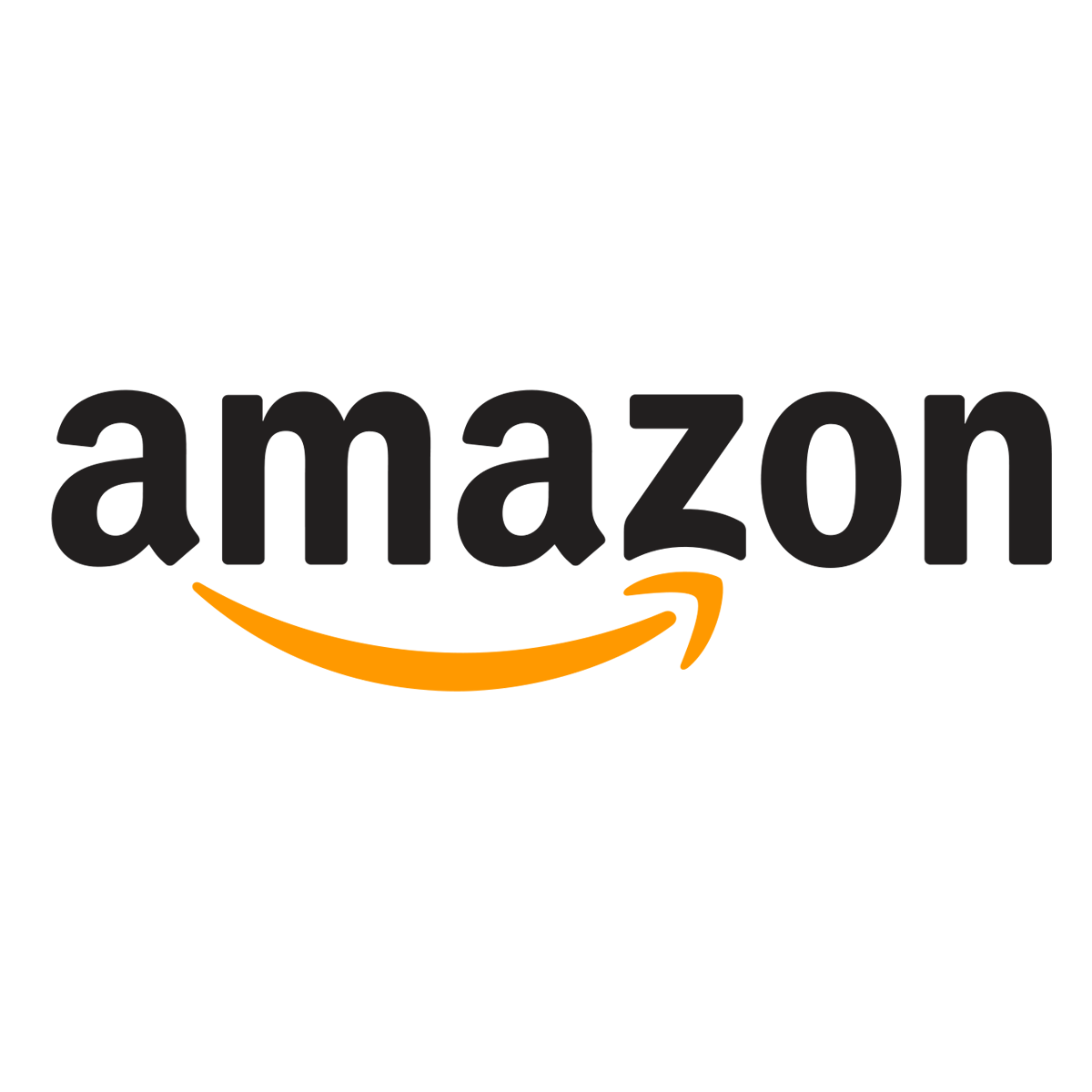
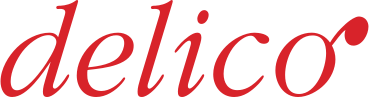
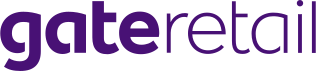
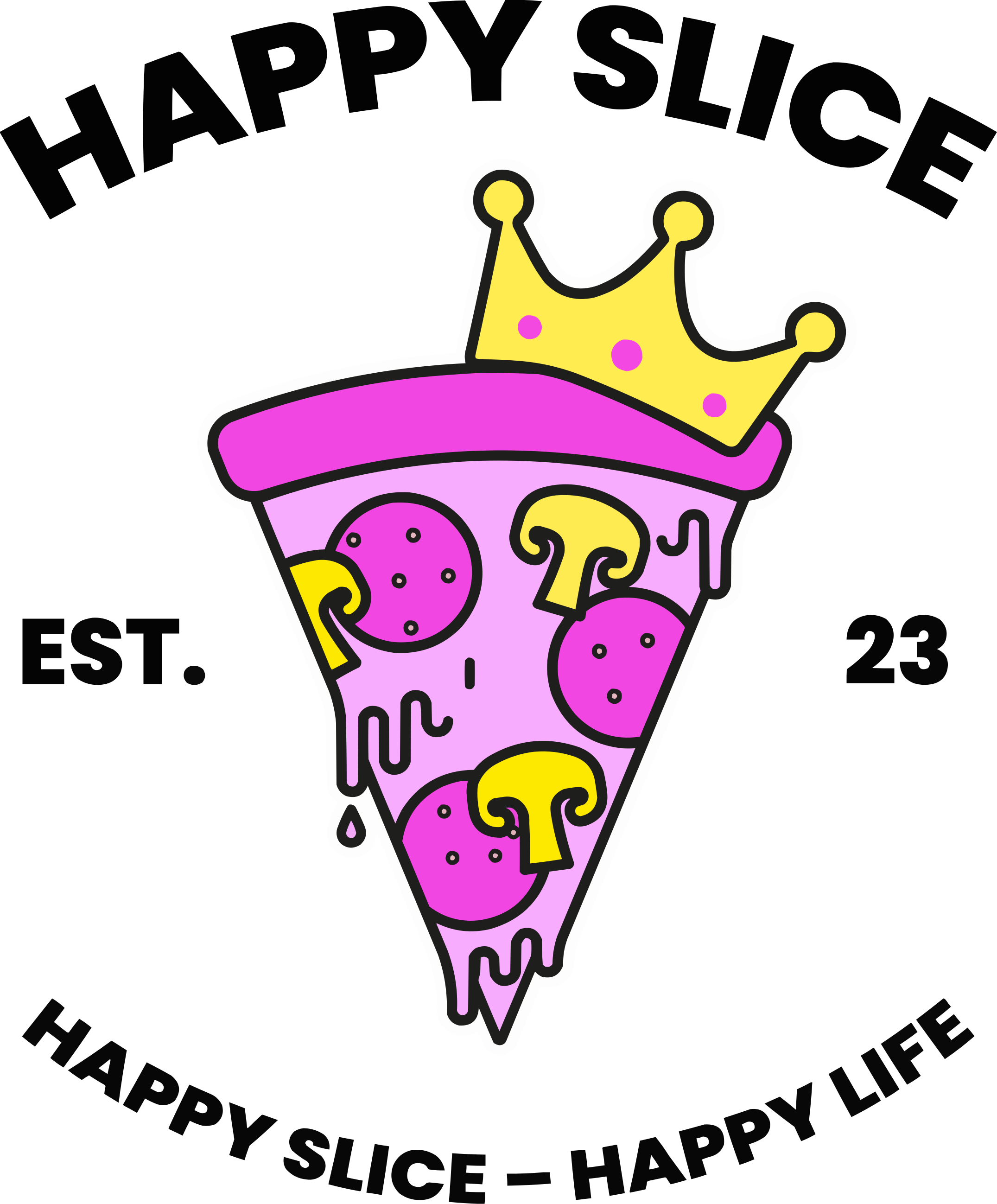
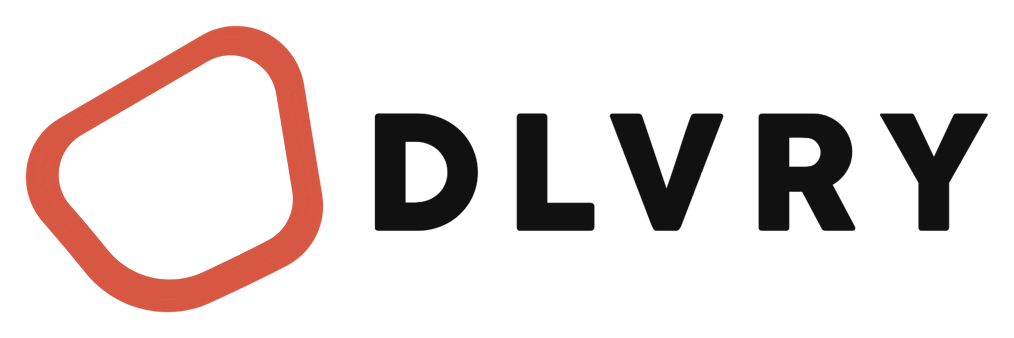
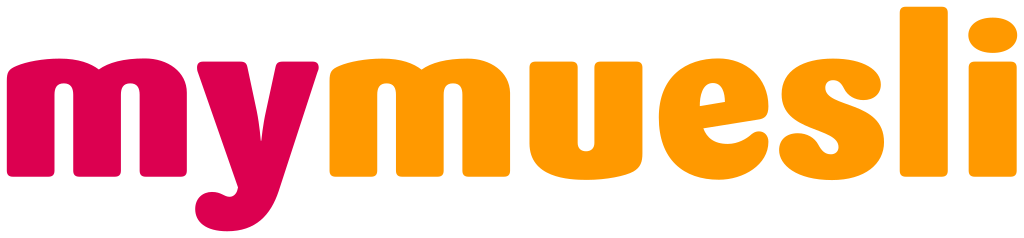
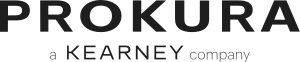
In highly regulated sectors like pharma and medical device manufacturing, product safety, quality, and conformity to federal regulations are most important. cGMP (Current Good Manufacturing Practices) certification is the gold standard in upholding industry standards and safeguarding consumers from harm from unsafe products.
This article is for pharmaceutical firms, medical device manufacturers, regulatory professionals, and industry experts who want to learn about cGMP certification, what's required, and how it can benefit them. With this certification, companies acquire a competitive edge, confirm supply chain authenticity, and are able to cope with the tough requirements of regulating authorities such as the FDA and the European Medicines Agency.
What is cGMP Certification?
Current Good Manufacturing Practices (cGMP) certification is a quality assurance standard that ensures pharmaceutical products, medical devices, and other regulated goods are consistently produced and controlled according to industry standards and regulatory policies.
It is issued by regulatory bodies such as the FDA and the European Medicines Agency (EMA) to confirm that a manufacturer complies with cGMP guidelines. This certification is essential for businesses involved in the manufacturing process of healthcare devices, pharmaceuticals, and other critical products to maintain compliance and ensure consumer safety.
Why cGMP Certification Matters?
Achieving cGMP certification is crucial for companies in the pharmaceutical and health technology industries to demonstrate adherence with regulatory requirements. It provides a competitive advantage by ensuring product safety, quality, and consistency. Additionally, it helps businesses navigate GMP audits and cGMP audits, minimizing risks of non-compliance and potential product recalls. Commitment to the Current Good Manufacturing Practices framework is also critical for businesses seeking international market access and public trust.
Benefits of cGMP Certification
Now that you understand the meaning and importance of cGMP certificate, it's time you learn the advantages and benefits of it.
- Ensures compliance with government mandates and regulatory: Regulatory authorities such as the FDA and EMA require implementation with the guidelines to ensure product safety and effectiveness.
- Enhances product quality and safety: Adhering to cGMP compliance ensures that pharmaceutical products and healthcare devices meet strict quality control measures, reducing risks of defects and contamination.
- Improves efficiency in the manufacturing process: Streamlining procedures through cGMP compliance enhances workflow, minimizes waste, and reduces errors.
- Reduces risks of contamination and defects: Strict adherence to sanitation and testing protocols helps prevent cross-contamination and ensures product consistency (International Society for Pharmaceutical Engineering, 2020).
- Strengthens consumer confidence and brand reputation: Customers trust brands that comply with the protocols, leading to increased market acceptance and credibility.
- Facilitates market access and business expansion: cGMP certification is often a prerequisite for exporting pharmaceutical products and medical tools to international markets.
Key Requirements for cGMP Certification
To obtain cGMP certification, businesses must meet stringent GMP requirements, including:
Documentation and Record-Keeping
Proper documentation is a critical aspect of cGMP compliance. Regulatory agencies require businesses to maintain detailed records of:
- Manufacturing processes: Records of every step in production, including batch records and process validation.
- Equipment maintenance and calibration: Regular documentation of maintenance schedules ensures consistent equipment performance.
- Training and certification: Training logs must be kept to confirm that personnel are qualified and up to date on cGMP requirements.
- Product testing and inspection results: Comprehensive records of testing data, stability studies, and quality control analyses are necessary for regulatory approval.
Personnel Qualification and Training
Training is essential for maintaining cGMP compliance. Training courses cover key aspects of current good manufacturing practices, cGMP requirements, and regulatory expectations. Properly trained personnel ensure that all Good Manufacturing Practices abidance and procedures are followed, reducing the risk of requirement violations, while also furthering their career advancement.
Facility and Equipment Standards
Facility and equipment standards are crucial for maintaining cGMP compliance. To begin with, manufacturing facilities must be designed to prevent contamination, ensuring a controlled environment for production. Additionally, equipment requires regular maintenance and calibration to uphold accuracy and efficiency. Moreover, strict sanitation and hygiene protocols further minimize risks and enhance product safety.
Quality Control and Testing Procedures
Quality control measures include routine testing, inspections, and and auditing of Good Manufacturing Practices. Third-party auditors may assess whether a manufacturer complies with regulatory framework and identify areas for improvement.
Supplier and Raw Material Management
Companies must ensure that raw materials meet cGMP regulations. Supplier qualification and monitoring processes help maintain product integrity and prevent contamination.
Industry-Specific cGMP Requirements
Regulatory authorities establish Current Good Manufacturing Practices based on market needs. For example:
- Medical device manufacturers must follow additional obligations for product safety
- Pharmaceutical companies must ensure that their new drug development processes align with cGMP standards
Regulatory Requirements for cGMP Certification
Regulatory requirements for Current Good Manufacturing Practices certification are essential for businesses producing pharmaceuticals, medical devices, and other regulated goods. To ensure alignment, regulatory authorities such as the FDA and EMA conduct routine inspections and audits. Companies must adhere to strict cGMP regulations, including proper documentation, facility management, and quality control. Failure to comply can result in penalties, recalls, or loss of market access.
cGMP vs. Other Quality Standards
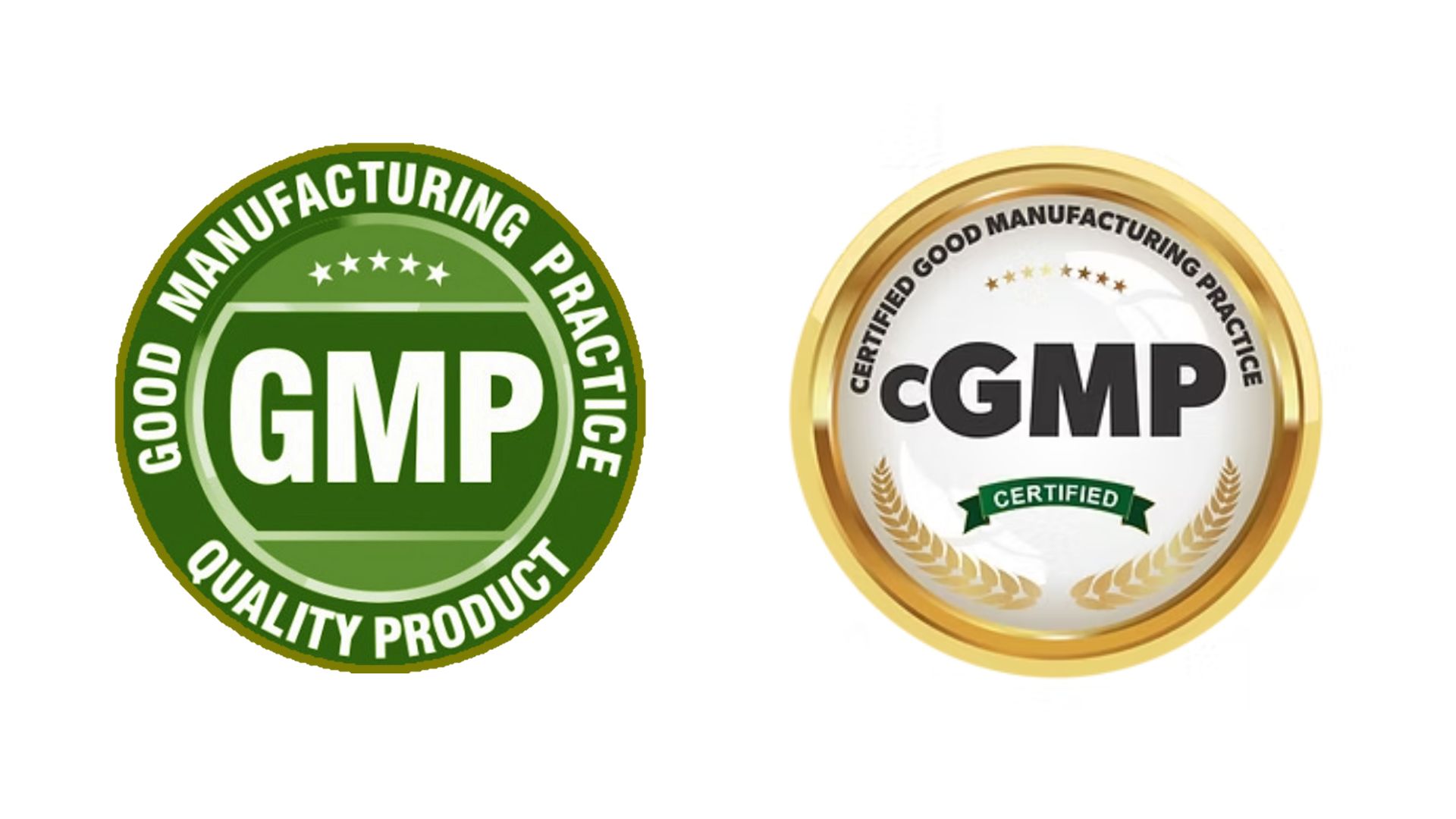
Understanding the differences between cGMP, GMP, and other quality standards is essential for businesses to select the most suitable certification.
cGMP vs. GMP
While GMP establishes fundamental good manufacturing practices and GMP compliance, cGMP incorporates modernized regulations emphasizing risk management, process validation, and continuous improvement. This makes cGMP more stringent, ensuring up-to-date implementation with evolving operational standards.
cGMP vs. ISO 9001
ISO 9001 focuses on general quality management systems applicable across industries, whereas cGMP specifically regulates pharmaceuticals and medical devices. ISO 9001 promotes efficiency and customer satisfaction, but it does not mandate compliance with regulatory bodies like the FDA or EMA.
cGMP vs. HACCP
HACCP (Hazard Analysis and Critical Control Points) is a preventive approach to food safety, focusing on identifying and controlling potential hazards in food production. In contrast, cGMP applies to pharmaceuticals and medical tools, requiring strict quality control, documentation, and adherence to regulatory requirements.
Which Certification Should Your Business Pursue?
Choosing the right certification depends on various factors, including industry type, regulatory obligations, and long-term market objectives. For pharmaceutical companies and medical device suppliers, cGMP ensures adherence with FDA and EMA regulations, while ISO 9001 may be more suitable for businesses seeking a general quality management system.
Additionally, HACCP is essential for food-related industries. Consulting with industry experts can provide valuable insights into the best certification path, helping organizations align with compliance requirements, improve operational efficiency, and gain a competitive edge in their respective markets.
The cGMP Certification Process
Obtaining this certification requires a structured approach, ensuring that companies meet regulatory requirements and standards at every stage of the process.
1. Planning, Training, and Internal Audits
The process begins with a thorough assessment of current practices to identify compliance gaps. Organizations must conduct staff training to ensure that employees understand cGMP standard and quality standards. Internal cGMP audits help evaluate readiness and highlight areas for improvement before undergoing external inspections.
2. Document Preparation
Comprehensive documentation is essential for compliance. Businesses must develop and maintain course materials that cover cGMP regulations, quality control measures, and operational procedures. Proper record-keeping ensures that all processes align with regulatory expectations and can withstand scrutiny during cGMP audits.
3. Third-Party Audits
A third-party auditor is engaged to conduct an external review of the organization’s adherence. This audit assesses whether the manufacturer follows the cGMP requirements. If deficiencies are found, corrective actions must be taken to address the identified issues before certification can be granted.
4. Corrective Actions and Compliance
Addressing non-compliance issues is a critical step. Organizations must implement corrective measures to resolve deficiencies identified during the cGMP audit. This may include revising procedures, enhancing quality control measures, or improving employee training programs to meet regulatory expectations.
5. Final Approval
Once all compliance requirements are met and corrective actions are verified, the organization undergoes a final evaluation. After successfully passing audits of Good Manufacturing Practices and demonstrating full adherence with cGMP laws, certification is awarded.
Cost and Time Required for cGMP Certification
The cost and time required for the certification depend on various factors, including company size, readiness, and regulatory requirements. Typically, the preparation phase takes several months, during which organizations conduct staff training, internal audits, and documentation updates. External audits by a third-party can further extend the process.
The costs include cGMP audit fees, internal preparation expenses, facility upgrades, and staff training programs. Long-term maintenance costs involve ongoing inspections, continuous training and development, and documentation updates. Despite the expenses, the certification is an investment in quality and regulatory commitment, ensuring market access and customer loyalty.
Conclusion
cGMP framework is a vital requirement for businesses involved in the production of pharmaceutical products and healthcare devices. By adhering to cGMP standard, businesses can ensure compliance, enhance product quality, and gain a competitive advantage in the market. Investing in training courses, internal audits, and regulatory compliance strategies is essential for long-term success and consumer trust.
Consider a small pharmaceutical startup that struggled with inconsistent product quality and regulatory setbacks. After investing in cGMP training and compliance measures, they not only improved their manufacturing process but also secured FDA approval, gaining credibility and expanding into new markets. This story highlights how Current Good Manufacturing Practices certification is more than just a regulatory requirement—it is a pathway to growth, trust, and excellence in the industry.