What is Batch Manufacturing Record? (With Examples)
What is batch manufacturing records or BMRs? Learn the ropes of process documentation, its benefits, key components, examples, challenges, and more!
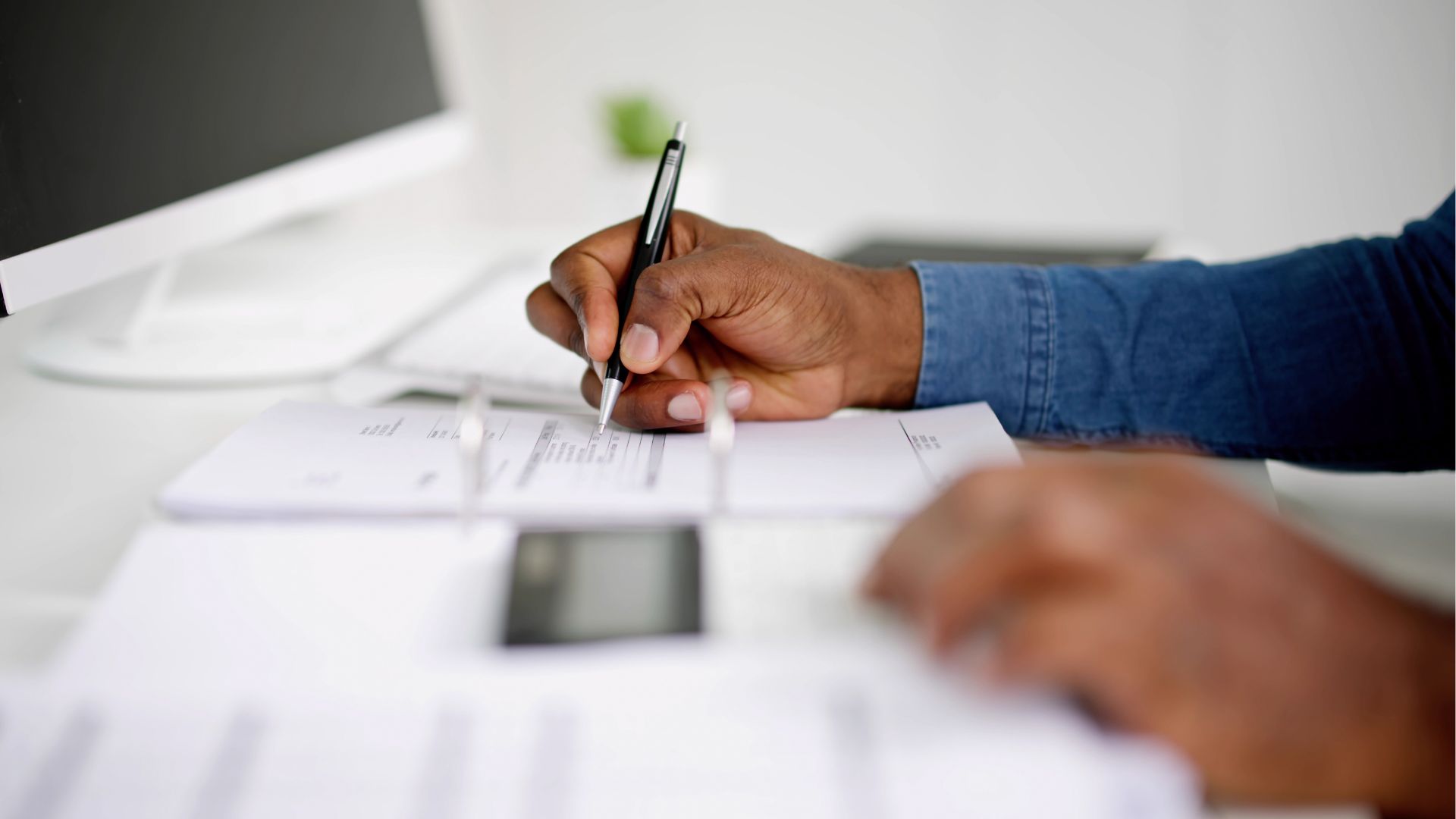
200+ buyers trust Torg for sourcing
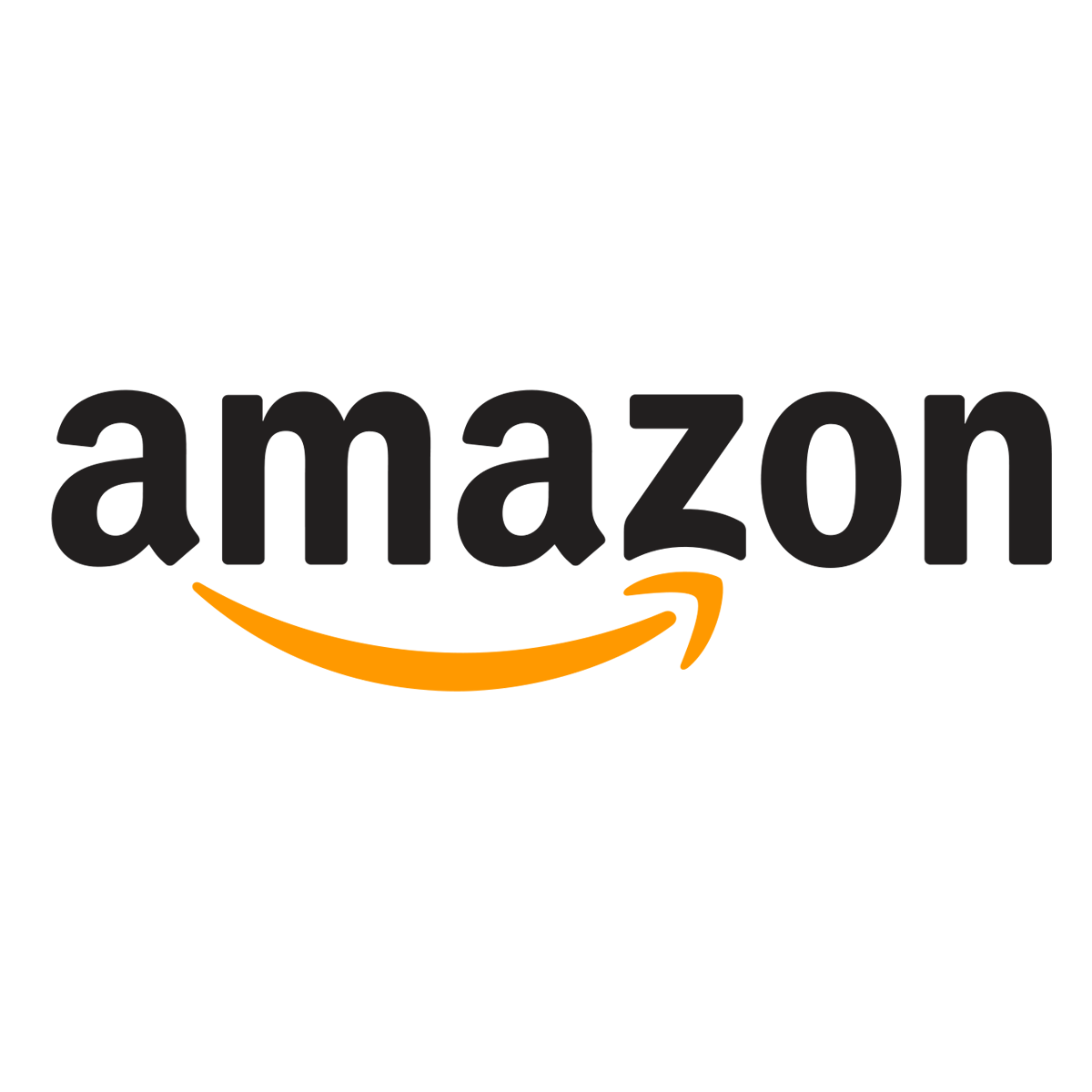
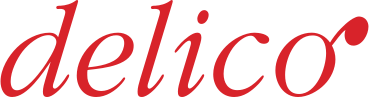
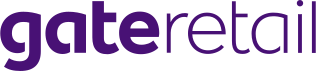
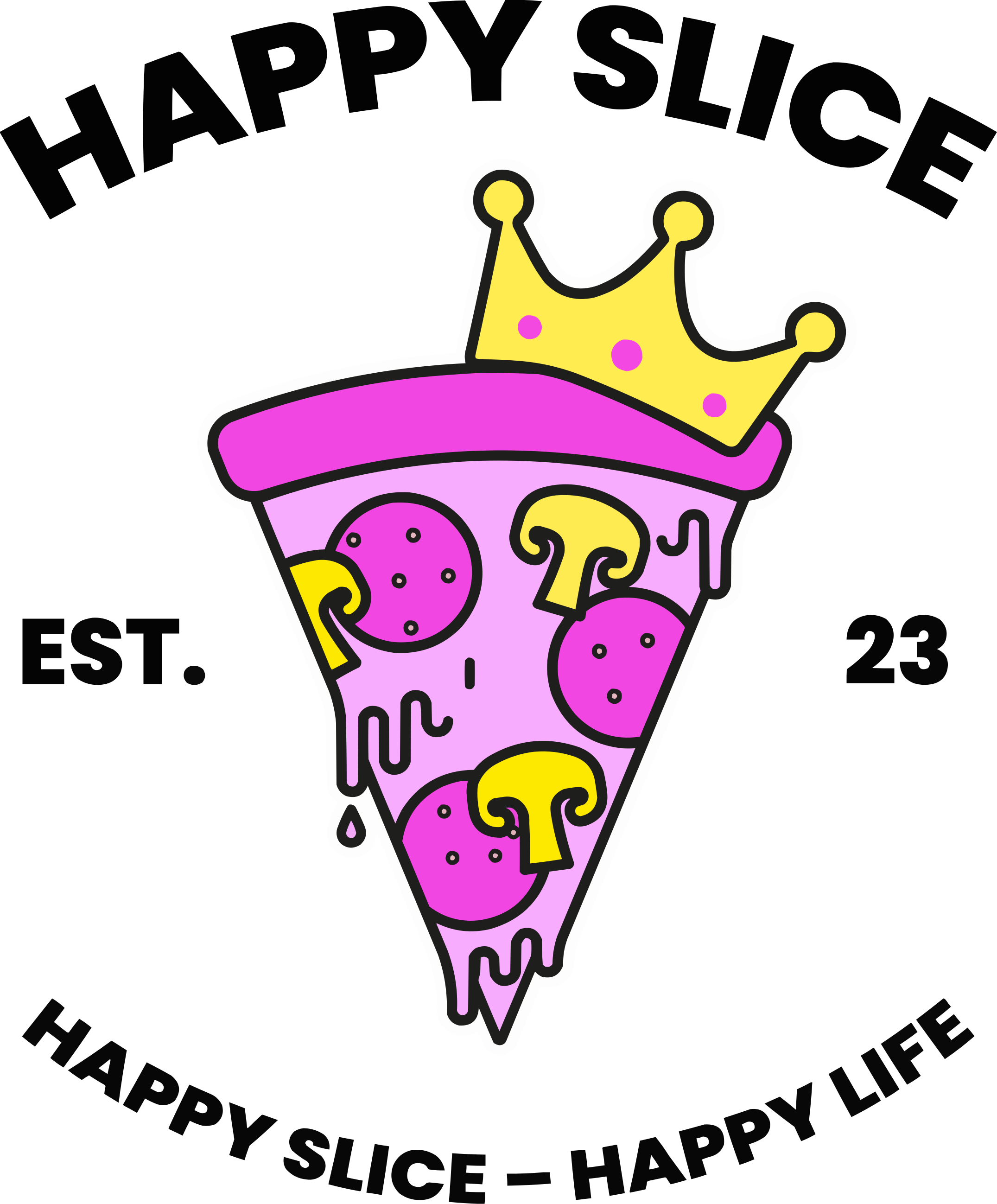
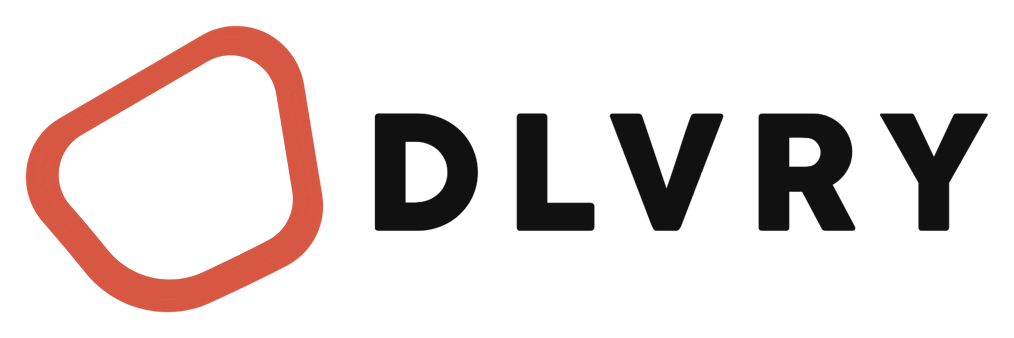
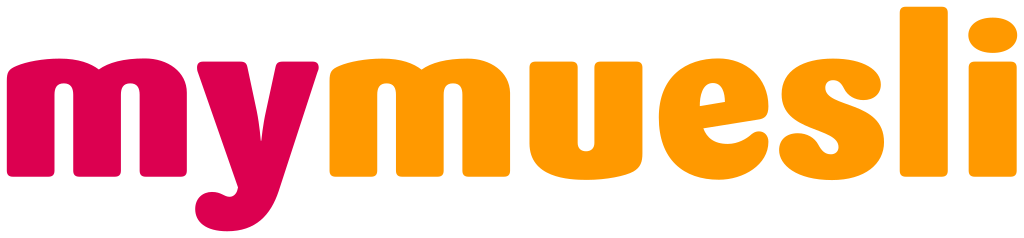
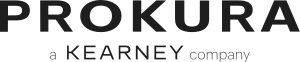
Batch Manufacturing Records (BMRs) are critical documents utilized in regulated industries like pharmaceuticals, food and beverage, cosmetics, and chemicals. They give a comprehensive description of the entire production process of each batch records to ensure adherence to Good Manufacturing Practices (GMP) and regulatory standards. BMRs assist manufacturers in ensuring product consistency, monitoring deviations, and enabling audits. This article discusses the significance of BMRs, their elements, and best practices for implementation and is an informative read for manufacturers, quality control staff, and regulatory experts.
What is Batch Manufacturing Record?
A Batch Manufacturing Record (BMR) is a detailed record of the entire manufacturing process a particular batch of a product. It is a serious document in industries that are regulated, including pharmaceuticals, food and beverages, cosmetics, and chemicals, where consistency of products and regulatory compliance are important.
BMRs give a step-by-step description of raw materials employed, equipment conditions, quality control checks, and the ultimate approval of batch records.
BMRs are important in manufacturing as they provide product consistency, uphold quality standards, and facilitate traceability. They assist in the detection and prevention of errors, regulatory compliance, and audit and inspection documentation.
BMRs are a fundamental part of GMP, where products are regularly manufactured and regulated in accordance with quality standards. They assist manufacturers in meeting regulatory requirements, for example, as set by the FDA, EMA, and other regulatory authorities.
A Master Formula Record (MFR) is a master document, giving standardized directions that detail the raw materials, operations, and quality control procedures needed to produce a batch of a product. The Batch Manufacturing Record (BMR), on the other hand, documents the actual implementation of the MFR, giving a real-time record of the entire manufacturing process.
The MFR has a thorough list of raw materials, equipment requirements, and sequential production process. On the other hand, the BMR captures real-world use of these detailed instructions, which may include modifications, deviations, and in-process quality inspections. Together, they ensure product quality, regulatory adherence, and process consistency.
BMRs give a step-by-step description of raw materials employed, equipment conditions, quality control checks, and the ultimate approval of batch records.
Key Function in the Manufacturing Process
BMRs are important in manufacturing as they provide product consistency, uphold quality standards, and facilitate traceability. They assist in the detection and prevention of errors, regulatory compliance, and audit and inspection documentation.
Relation to Good Manufacturing Practices (GMP)
BMRs are a fundamental part of GMP, where products are regularly manufactured and regulated in accordance with quality standards. They assist manufacturers in meeting regulatory requirements, for example, as set by the FDA, EMA, and other regulatory authorities.
Master Formula Records (MFRs) and Batch Manufacturing Records
A Master Formula Record (MFR) is a master document, giving standardized directions that detail the raw materials, operations, and quality control procedures needed to produce a batch of a product. The Batch Manufacturing Record (BMR), on the other hand, documents the actual implementation of the MFR, giving a real-time record of the entire manufacturing process.
The MFR has a thorough list of raw materials, equipment requirements, and sequential production process. On the other hand, the BMR captures real-world use of these detailed instructions, which may include modifications, deviations, and in-process quality inspections. Together, they ensure product quality, regulatory adherence, and process consistency.
Benefits of Using Batch Manufacturing Records
Regulatory Compliance
BMRs ensure manufacturing processes adhere to Good Manufacturing Practices (GMP) and comply with regulatory guidelines of agencies such as the FDA and EMA. Documentation avoids compliance breaches and guarantees product safety and quality for chemical and process manufacturers.
Product Consistency
Uniformity in various batch production records is essential in sectors like pharmaceuticals manufacturing process, food, and cosmetics. BMRs offer a systematic method for documenting manufacturing processes, guaranteeing each batch complies with specified quality standards as defined in the master production records.
Traceability
BMRs provide an exhaustive record of production, which makes it possible to trace each batch. Such records are vital in case of audits, recalls, and settling any quality concerns raised after delivery.
Quality Control
By maintaining documentation of monitoring and quality control testing at real-time, BMRs verify that the product adheres to specified quality specifications at every stage. Corrective actions and checks during in-process are documented in order to preserve consistency and safety.
Error Reduction
Precise step-by-step guidelines in BMRs ensure reduced human mistakes and avoid variations. If any variations take place, they are immediately recorded and corrected within the batch production records to prevent defects and violations.
Key Components of a Batch Manufacturing Record
- Product Information: This section contains mandatory information like the product name, identification code, batch number, and manufacture date. This information facilitates traceability and efficient tracking of each batch production. Chemical and process manufacturers rely on these records to ensure consistency and compliance.
- Process Manufacturing Instructions: This section details the step-by-step manufacturing protocols that have to be adhered to in order to maintain uniformity in the batch production process. It describes the order of operations, the mixing times, and the critical control points outlined in the master production records.
- Material Specifications: A batch manufacturing record (BMR) includes a list of all raw materials applied in production, their needed quantities, and quality standards they need to adhere to. This ensures that only approved and quality materials are applied in chemical and process manufacturing.
- Equipment and Settings: It records all the equipment applied in manufacturing, including particular operating settings like temperature, pressure, and mixing speeds. This ensures that machines are properly set up to meet the quality standards documented in the master batch record.
- Quality Control Tests: The file contains all specifications required for testing, including in-process quality inspections. This guarantees that the product is up to standard at different stages of production prior to final release and that future batches will maintain the same quality.
- Batch Documentation: This section holds records of all inspections, production process changes, and approvals made during production. It is an official document confirming that the batch has been produced according to all necessary protocols and regulations in compliance with batch production records.
Examples of Batch Manufacturing Records
Fruit Juice
- Batch Record Title: Orange Juice Production Batch Record
- Batch Number: FJ2025-01
- Date of Manufacture: February 15, 2025
- Materials Used:
- Fresh Oranges (Batch #OR2345)
- Sugar (Batch #SU5678)
- Citric Acid (Batch #CA9012)
- Water (Batch #W2345)
- Fruit Preparation: Wash and peel 1,000 kg of oranges.
- Juicing: Extract juice using hydraulic press.
- Pasteurization: Heat juice to 85°C for 5 minutes to kill microorganisms.
- Blending: Add sugar and citric acid, blend for 10 minutes.
- Packaging: Fill in 1-liter bottles.
- In-Process Testing:
- Brix Level: 12° Brix.
- Acidity: 0.5%.
Shampoo Production
- Batch Record Title: Herbal Shampoo Production Record
- Batch Number: SHP-450
- Date of Manufacture: February 20, 2025
- Materials Used:
- Surfactants: Sodium Lauryl Sulfate (Batch #SLS345)
- Herb Extract: Aloe Vera Extract (Batch #Aloe567)
- Preservative: Phenoxyethanol (Batch #Phen891)
- Water (Batch #W123)
- Ingredient Preparation: Weigh 200 kg of surfactants and 50 kg of aloe vera extract.
- Mixing: Mix ingredients in a stainless-steel tank for 15 minutes at 250 RPM.
- Heating: Heat mixture to 70°C for 20 minutes.
- Homogenization: Homogenize for 5 minutes at 3000 RPM.
- Cooling: Cool mixture to room temperature.
- Packaging: Fill 500 ml bottles with shampoo.
- In-Process Testing:
- pH: pH 5.5-6.5.
- Viscosity: 5000 centipoise.
How to Create and Maintain a Batch Manufacturing Record
1. Planning & Preparation
First, product specifications, formulation information, and the efficient production workflow as a whole need to be defined. This is where required documentation is collected, such as Standard Operating Procedures (SOPs), master batch records, and raw material specifications. Responsibilities also need to be allocated to production and quality control personnel to ensure that operations run smoothly.
2. Designing the Batch Manufacturing Record
The second step is to create a complete BMR template containing all the necessary sections. It is important to add regulatory needs in order to meet Current Good Manufacturing Practices (cGMP) requirements as well as those guidelines established by the U.S. Food and Drug Administration (FDA) and the European Medicines Agency. An organized template makes record-keeping precise and compliant with regulations.
3. Approval and Training
After designing the BMR template, review and approval must take place in association with regulatory and quality assurance staff. Suitable training should be issued to staff regarding proper and traceable documentation procedure so that everything entered is precise, clear, and verifiable.
4. Batch Manufacturing Process
In the manufacturing process, all raw materials, packaging, and equipment utilized must be documented. Detailed and clear-cut instructions are required, including in-process inspection to ensure quality and consistency at every step.
5. Batch Record Execution
The manufacturing process, including the duration, temperature, and any procedure deviation, has to be scrupulously documented. Further, in-process inspection and its outcomes need to be recorded for retaining product quality. Documenting things in this way makes things clear and facilitates regulation adherence.
6. Quality Assurance & Review
Once production is completed, the in-process data should be checked to ensure compliance with set standards. All non-conformities that are found should be dealt with and corrected immediately. A systematic process of review ensures high-quality standards and reduces risks.
7. Final Documentation & Batch Release
All sections of the BMR must be completed accurately before a batch can be released. Quality control approval is required to confirm that the batch complies with all the necessary specifications. This is an important step in regulatory compliance and product safety.
8. Archiving and Record Maintenance
Lastly, finished batch manufacturing records must be stored safely for traceability and future reference. Regular review of records enables process improvements and continued compliance with regulatory requirements. Efficient record maintenance promotes operational efficiency and compliance.
Batch Manufacturing Record Compliance and Regulations
There are a number of authorities that regulate Batch Manufacturing Record compliance to guarantee adherence to industry standards. The U.S. Food and Drug Administration (FDA), European Medicines Agency (EMA), and World Health Organization (WHO) have key roles in the regulation of pharmaceutical, food, and other manufacturing industries. These organizations establish guidelines to ensure consistency and avoid manufacturing process discrepancies.
Key Compliance Standards
Various industries are required to adhere to certain regulatory guidelines in order to ensure operational legitimacy. In the pharmaceutical manufacturing, adherence to 21 CFR Part 211 guarantees that drug products comply with quality and safety requirements. The food sector uses Hazard Analysis and Critical Control Points (HACCP) guidelines for preventing contamination and maintaining food safety. Furthermore, different industries conform to International Organization for Standardization (ISO) standards, which ensure elaborate guidelines for quality management and safety.
Regulatory Penalties and Fines
Non-compliance with batch manufacturing documentation requirements has serious implications, such as regulatory penalties, product recall, and possible legal prosecution. Non-compliance can also attract huge monetary fines, negative publicity, and even plant closures. To avoid risks, manufacturers have to ensure comprehensive and accurate documentation, periodic audits, and strict compliance with compliance standards.
By adhering to these guidelines of regulation, organizations can maintain quality assurance, prevent legal sanctions, and keep consumer confidence in their products.
Key Compliance Standards
Various industries are required to adhere to certain regulatory guidelines in order to ensure operational legitimacy. In the pharmaceutical manufacturing, adherence to 21 CFR Part 211 guarantees that drug products comply with quality and safety requirements. The food sector uses Hazard Analysis and Critical Control Points (HACCP) guidelines for preventing contamination and maintaining food safety. Furthermore, different industries conform to International Organization for Standardization (ISO) standards, which ensure elaborate guidelines for quality management and safety.
Regulatory Penalties and Fines
Non-compliance with batch manufacturing documentation requirements has serious implications, such as regulatory penalties, product recall, and possible legal prosecution. Non-compliance can also attract huge monetary fines, negative publicity, and even plant closures. To avoid risks, manufacturers have to ensure comprehensive and accurate documentation, periodic audits, and strict compliance with compliance standards.
By adhering to these guidelines of regulation, organizations can maintain quality assurance, prevent legal sanctions, and keep consumer confidence in their products.
Common Challenges in Batch Manufacturing Record Management
Proper management of Batch Manufacturing Records is most important for regulatory adherence, product quality, and operational efficiency. Nevertheless, a number of challenges may be encountered in keeping accurate and reliable records. Some of the most common challenges in BMR management are as follows.
Traditional paper-based BMRs are vulnerable to human errors, misplacement, and data retrieval inefficiencies. Unlike these, computer-based record-keeping systems ensure improved accuracy, better traceability, and quicker data access in real-time. Adoptions of electronic BMR (eBMR) systems have the capability to significantly mitigate transcription error risk and compliance work.
Manufacturing discrepancies and departures from approved production processes can affect product quality and compliance with regulatory requirements. Careful documentation of the deviations, including root cause analysis and corrections, is necessary to ensure process integrity. A well-established deviation management system helps guarantee that deviations are addressed and closed in a timely manner.
Protection of BMRs from unauthorized access, tampering, or loss is one of the biggest challenges, particularly in computerized systems. Strict access control, data encryption, and recurrent audits must be put in place by companies to ensure record integrity. Compliance with data protection laws like 21 CFR Part 11 and ISO 27001 is critical in the security of sensitive manufacturing information.
As the production volume increases, it becomes more challenging to manage BMRs for large-scale operations. The use of standardized procedures, automation, and enterprise resource planning (ERP) systems can assist organizations in managing large-scale manufacturing records efficiently. Scalable solutions ensure consistency and compliance across various production lines.
Manual vs. Digital Record-Keeping Challenges
Traditional paper-based BMRs are vulnerable to human errors, misplacement, and data retrieval inefficiencies. Unlike these, computer-based record-keeping systems ensure improved accuracy, better traceability, and quicker data access in real-time. Adoptions of electronic BMR (eBMR) systems have the capability to significantly mitigate transcription error risk and compliance work.
Handling Discrepancies and Deviations
Manufacturing discrepancies and departures from approved production processes can affect product quality and compliance with regulatory requirements. Careful documentation of the deviations, including root cause analysis and corrections, is necessary to ensure process integrity. A well-established deviation management system helps guarantee that deviations are addressed and closed in a timely manner.
Maintaining Security and Integrity of BMR Data
Protection of BMRs from unauthorized access, tampering, or loss is one of the biggest challenges, particularly in computerized systems. Strict access control, data encryption, and recurrent audits must be put in place by companies to ensure record integrity. Compliance with data protection laws like 21 CFR Part 11 and ISO 27001 is critical in the security of sensitive manufacturing information.
Scaling BMR Processes in Large Manufacturing Operations
As the production volume increases, it becomes more challenging to manage BMRs for large-scale operations. The use of standardized procedures, automation, and enterprise resource planning (ERP) systems can assist organizations in managing large-scale manufacturing records efficiently. Scalable solutions ensure consistency and compliance across various production lines.
Industry-Specific Considerations for Batch Manufacturing Records
Batch Manufacturing Records (BMRs) are important to ensure product quality, regulatory requirements, and traceability in all industries. All industries have different requirements that have to be met for maintaining operating efficiency and regulatory adherence.
The pharmaceutical sector operates under strict regulatory systems enforced by the U.S. Food and Drug Administration (FDA) and the European Medicines Agency (EMA). BMRs are required to provide detailed documentation for product recalls, quality control specifications, and confirmation of compliance with Current Good Manufacturing Practices (cGMP). Keeping accurate records of ingredients, batch records, batch numbers, and test results is necessary to ensure product safety and efficacy.
Food safety depends on compliance with regulatory requirements like Hazard Analysis and Critical Control Points (HACCP), FDA, and U.S. Department of Agriculture (USDA) regulations. BMRs within this industry have to maintain meticulous ingredient lists, processing procedures, and allergen controls to ensure minimal contamination threats and consumer protection. Proper traceability also makes it easier for product recalls to be carried out if needed.
Cosmetic manufacturers have to adhere to FDA and EU Cosmetic Regulation (EC 1223/2009) regulations. BMRs are required for the monitoring of preservatives, pH levels, and microbiological stability to maintain product safety and consistency. Documentation also needs to outline formulation adjustments, packaging components, and stability testing to satisfy international requirements. Also, using electronic batch records can streamline documentation and compliance verification
Batch records in the chemical industry are required to record handling, use of hazardous chemicals, and process manufacturing to conform to Occupational Safety and Health Administration (OSHA), Environmental Protection Agency (EPA), and Registration, Evaluation, Authorization, and Restriction of Chemicals (REACH) laws. Proper safety procedures, labeling, storage requirements, and waste disposal need to be accurately documented to reduce health and environmental hazards.
Pharmaceutical Industry
The pharmaceutical sector operates under strict regulatory systems enforced by the U.S. Food and Drug Administration (FDA) and the European Medicines Agency (EMA). BMRs are required to provide detailed documentation for product recalls, quality control specifications, and confirmation of compliance with Current Good Manufacturing Practices (cGMP). Keeping accurate records of ingredients, batch records, batch numbers, and test results is necessary to ensure product safety and efficacy.
Food and Beverage Industry
Food safety depends on compliance with regulatory requirements like Hazard Analysis and Critical Control Points (HACCP), FDA, and U.S. Department of Agriculture (USDA) regulations. BMRs within this industry have to maintain meticulous ingredient lists, processing procedures, and allergen controls to ensure minimal contamination threats and consumer protection. Proper traceability also makes it easier for product recalls to be carried out if needed.
Cosmetics and Personal Care
Cosmetic manufacturers have to adhere to FDA and EU Cosmetic Regulation (EC 1223/2009) regulations. BMRs are required for the monitoring of preservatives, pH levels, and microbiological stability to maintain product safety and consistency. Documentation also needs to outline formulation adjustments, packaging components, and stability testing to satisfy international requirements. Also, using electronic batch records can streamline documentation and compliance verification
Chemical Industry
Batch records in the chemical industry are required to record handling, use of hazardous chemicals, and process manufacturing to conform to Occupational Safety and Health Administration (OSHA), Environmental Protection Agency (EPA), and Registration, Evaluation, Authorization, and Restriction of Chemicals (REACH) laws. Proper safety procedures, labeling, storage requirements, and waste disposal need to be accurately documented to reduce health and environmental hazards.
Conclusion
Batch Manufacturing Records are critical to ensuring product quality, regulatory adherence, and traceability in chemical and process manufacturing businesses. Following guidelines in documentation processes will ensure greater efficiency, minimize errors, and satisfy regulatory needs. The changeover to computerized BMR systems can actually make the batch process even easier and minimize risks to compliance.