Pegging in Supply Chain: A Complete Guide
Pegging in supply chain helps businesses trace demand back to its source, optimizing inventory and production. Learn how it improves efficiency and planning.
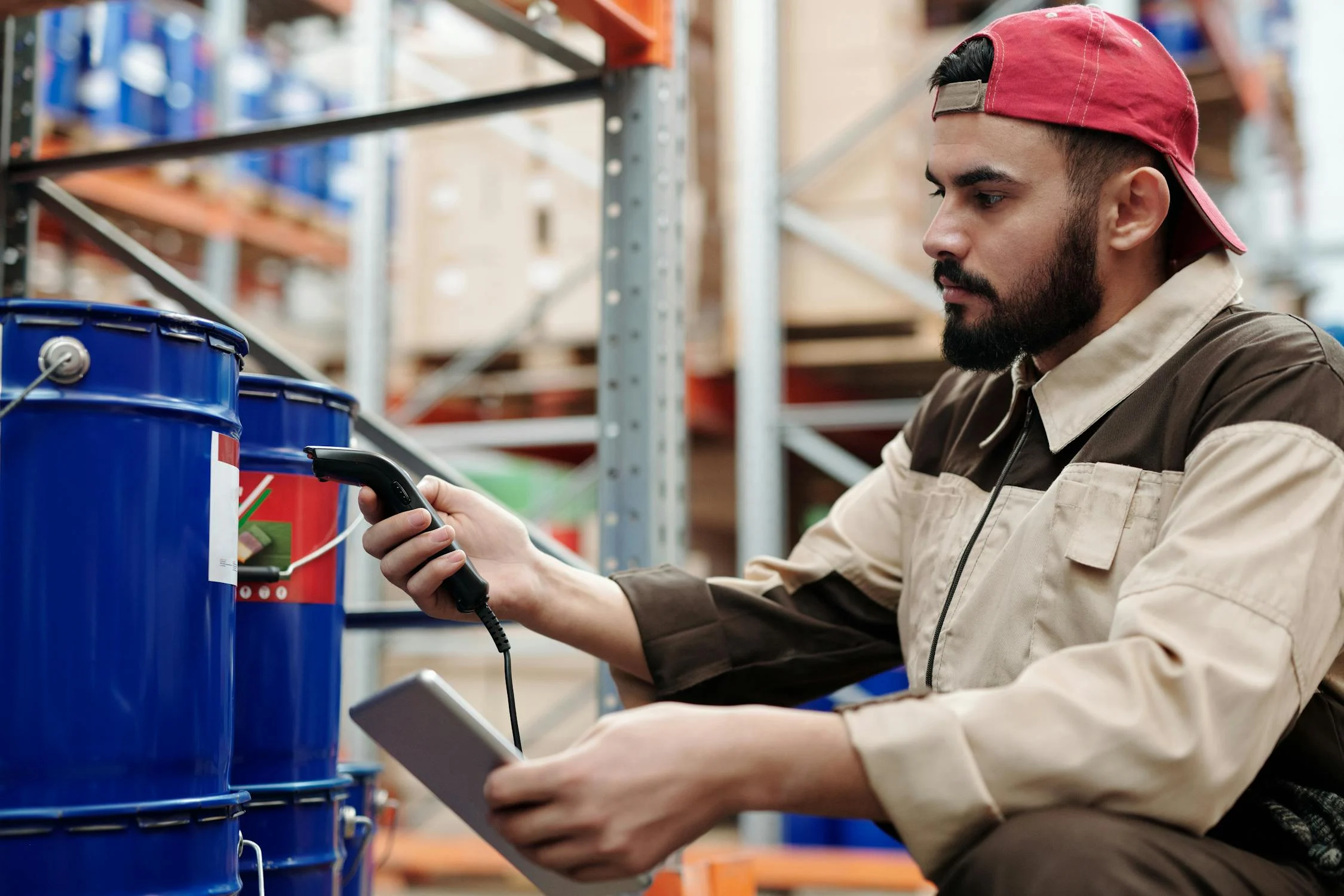
200+ buyers trust Torg for sourcing
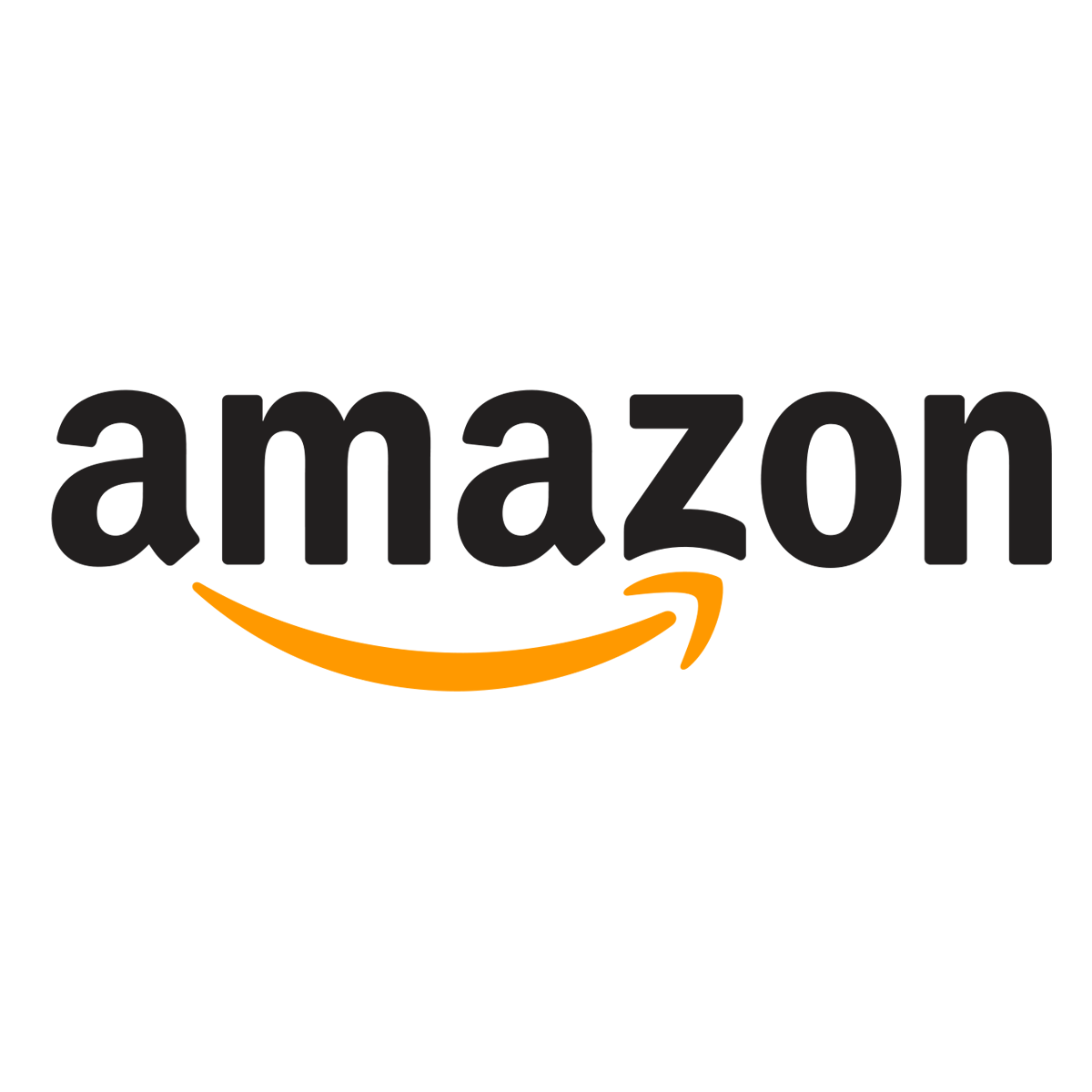
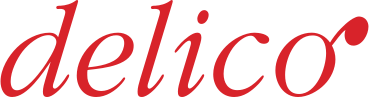
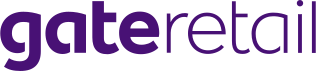
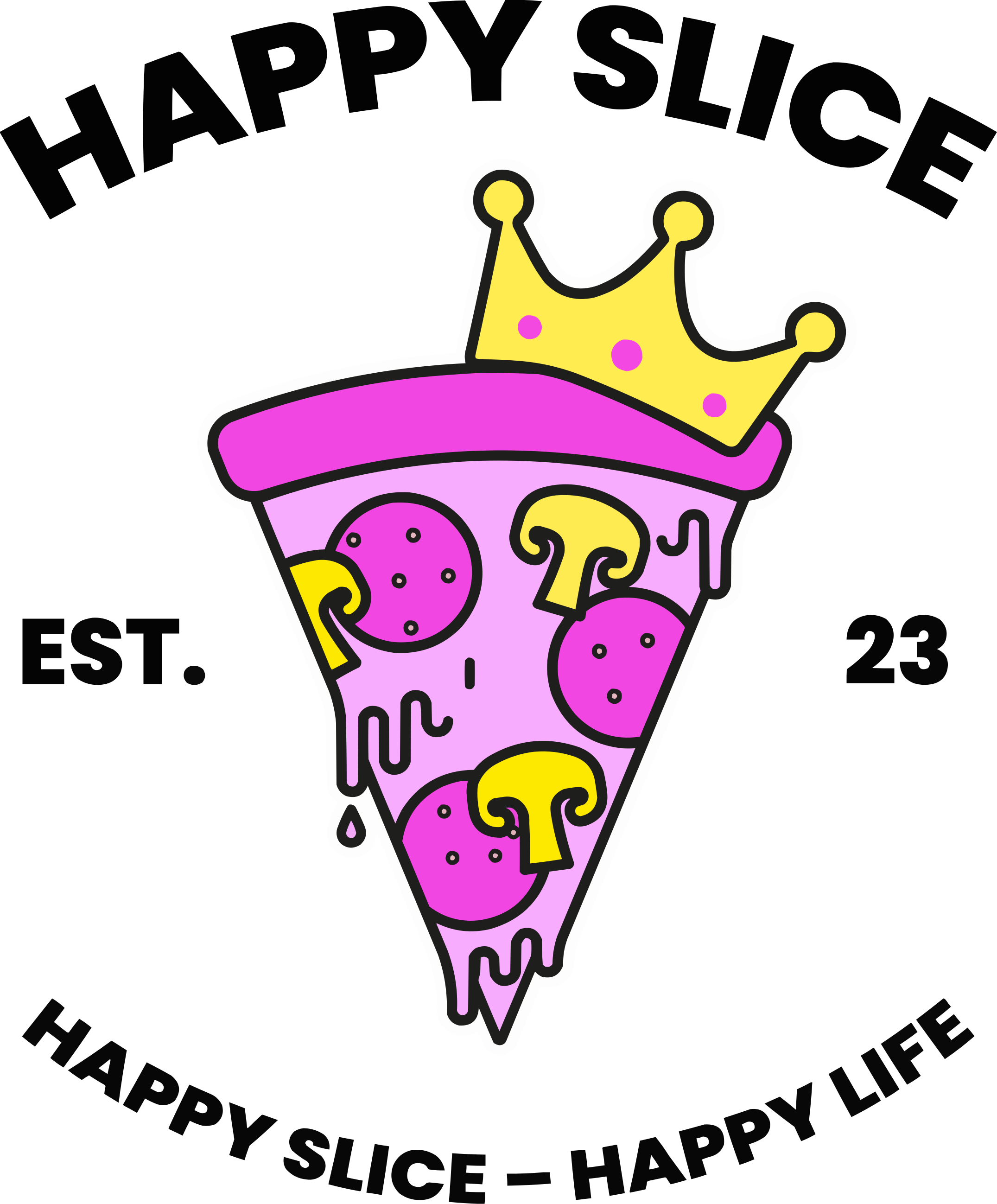
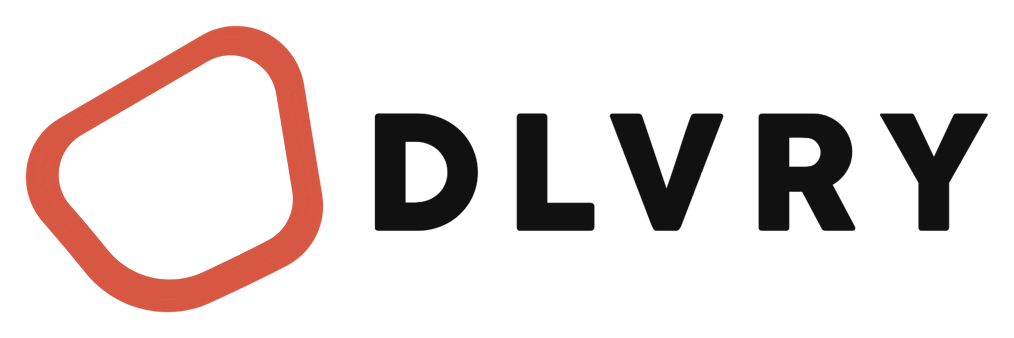
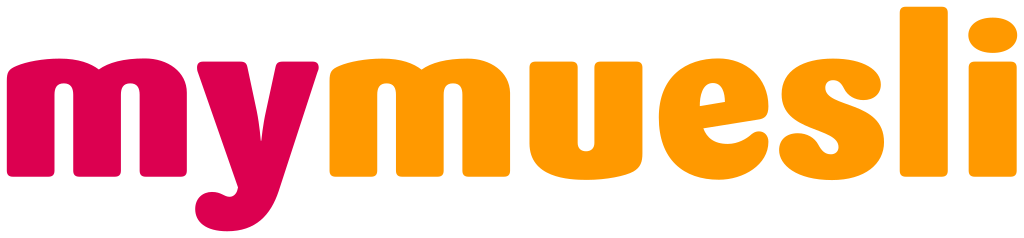
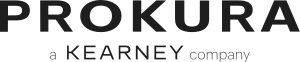
Pegging in Supply Chain: A Complete Guide
Companies must stay ahead of the game by having accurate demand planning, good inventory management, and cost savings. That’s where pegging in the supply chain comes in—a technique that allows companies to track demand back to its source, giving them visibility into production, and procurement activities.
Say you have a factory that produces thousands of units a day, and then you get an emergency order that needs raw materials you’re already running low on. How do you know which supplier shipment or stock can meet this requirement without impacting current operations? Pegging solves this by knowing which inventory or purchase order is tied to a particular demand, so the decision is more accurate.
In this guide, we will break down what pegging is, why it’s important, how it works, its types, benefits, and practical applications in manufacturing, retail, and automotive. As a procurement manager, supply chain analyst, or business person, this will show you how pegging can improve your supply chain and give you a competitive edge.
What is Pegging in the Supply Chain?
Pegging in the supply chain refers to the process of tracking and linking individual customer orders or production requirements to specific components or raw materials within the supply chain. It involves identifying which supplies, components, or materials are required to fulfill a particular customer order or production demand.
For example, when a retailer sees higher sales of an item, pegging identifies the demand and traces it back to warehouse stock, purchase orders, or raw materials that need to be procured to fulfill the demand.
Pegging is also used in Material Requirements Planning (MRP) and Enterprise Resource Planning (ERP) systems to ensure production and stock levels match market demand.
Join Torg today to connect with top-tier manufacturers and suppliers in the food and beverage industry. Get started now and elevate your supply chain with the right connections!
Key Functions of Pegging in Supply Chain
- Traceability: Determines which supply (inventory, raw materials or purchase orders) is fulfilling specific demand.
- Efficiency: Avoids overstocking and understocking by matching supply with real needs.
- Decision-making: Enables companies to allocate resources efficiently and react to market changes fast.
Why is Pegging Important in the Modern Supply Chain?
In today’s fast-paced, globally connected supply chain companies have to balance volatile demand, supplier risks, and inventory control—and that’s no fun. With just-in-time (JIT) manufacturing, even a minor disruption can cause missed deadlines, lost sales, or dissatisfied customers, making pegging an essential tool to keep everything in harmony.
Here’s why it’s important:
- Optimize Inventory: Pegging ensures each unit of stock is assigned exactly where it’s needed and there’s no stock shortages or over-buying.
- Minimize Waste: By linking demand to supply companies avoid unwanted production and elimination of excess inventory.
- Maximize Forecasting: Up-to-date monitoring enables supply chain managers to forecast demand changes and make informed planning decisions.
- Boost Customer Satisfaction: By guaranteeing on-time order execution pegging enables companies to deliver on promises and prevent backorders.
- Supplier Coordination: It allows manufacturers and suppliers to be in sync by tracing demand changes back to the source, improving collaboration.
For industries like manufacturing, retail, and automotive—where supply chains have multiple suppliers and stages—pegging ensures smooth operation, cost savings, and responsiveness to market changes. It’s not just about tracking materials; it’s about making better, faster, and more reliable supply chain decisions.
Types of Pegging in Supply Chain
Pegging can be broken down into two types:
1. Backward Pegging
Backward pegging traces demand back to its source supply, helping businesses identify where raw materials or inventory originate and ensuring they meet production needs efficiently.
Example: A car manufacturer gets an order for 500 vehicles. Using backward pegging, they can track which raw materials (steel, tires, engines) were allocated for this order and if there are any shortfalls.
2. Forward Pegging
Forward pegging tracks available supply to future demand, allowing businesses to allocate resources effectively and anticipate potential shortages or surpluses.
Example: A retailer gets a new batch of gaming consoles. With forward pegging, they can see which customer orders will be fulfilled with this inventory.
They are different but both are definitely essential for supply-demand alignment across the entire supply chain.
How Pegging Works in the Supply Chain
At its core, pegging is like having a live inventory detective in your supply chain—it tracks and links demand to supply so everything flows. Companies use MRP (Material Requirements Planning) and ERP (Enterprise Resource Planning) systems to automate this process, remove the guesswork, and make informed decisions.
Here’s how it works:
- Demand Identification: The system recognizes a specific order, production schedule, or forecasted need and the material or product required.
- Link to Supply: It then matches that demand to available inventory, raw materials, or purchase orders and ensures everything is accounted for.
- Tracking Dependencies: Pegging ensures each supply source is properly allocated so there’s no shortages or overstocking that can disrupt operations.
- Real Time Updates: If demand changes—say an increase in customer orders or supplier delay—the system dynamically adjusts the supply allocation to keep everything flowing.
Let’s say an automotive manufacturer suddenly runs out of engine components. Instead of trying to figure out where the problem is, pegging tells which supplier deliveries are impacted and which vehicle models will be delayed. With that information, the manufacturer can prioritize critical orders, expedite shipments, or adjust production schedules without disrupting anything. In essence, pegging is the invisible traffic cop of the supply chain ensuring every part and product ends up exactly where it’s needed, on time.
Pegging vs. Traditional Supply Chain Management
Pegging in supply chain management is a more precise and live approach than traditional supply chain. Traditional supply chain management is all about breadth of inventory planning, while pegging is about tracing demand back to its supply source. So every piece of stock is allocated based on actual requirement rather than forecast.
Decision making is also data driven and responsive with pegging. Traditional supply chain is all about bulk inventory planning which can lead to overstocking or stockout. Pegging is about real-time tracking so you can adjust supply allocation as demand changes. That’s why it’s super useful in industries with fluctuating market demand like manufacturing and retail.
Another big difference is flexibility and adaptability. Traditional supply chains follow fixed procurement and production schedules which makes it harder to respond to sudden changes. Pegging allows you to prioritize urgent orders and adjust production schedules dynamically. That’s how you can be more efficient, reduce waste, and improve cost management.
In the end, pegging changes the way your supply chain operates by making it agile, transparent, and demand-driven. That's a big advantage over traditional inventory and production management.
Benefits of Pegging in Supply Chain Management
Pegging has many benefits from better demand planning to cost savings. Here’s how it helps:
1. Forecasting and Demand Planning
By knowing which sources supply which demands, you can make accurate predictions, and avoid stockouts or overstocking. This means smoother production flow and better alignment to customer needs.
2. Visibility and Traceability
Pegging gives you real time tracking, so you can see where raw materials, components, or finished goods are allocated. This transparency helps you reduce errors, prevent stockouts, and comply with industry regulations.
3. Better Decision Making
With pegging you can prioritize urgent orders, allocate resources efficiently, and adjust production schedule based on real demand. This means faster response time, shorter lead time, and better customer satisfaction.
4. Reduced Waste and Inventory Costs
Pegging minimizes overproduction and excess stock which means lower storage costs and reduced financial risks. By only buying what’s needed for specific demand, you can cut down waste, and obsolete inventory.
Applications of Pegging in Supply Chains
Different industries use pegging to make supply chain operations more efficient. Here’s how it’s used in key sectors:
1. Pegging in Manufacturing
Manufacturers use pegging to track raw materials and component usage to ensure smooth production and no downtime. This helps to keep production schedules consistent and prevent bottlenecks on the production line.
2. Pegging in Retail Supply Chains
Retailers use pegging to match shipments to customer orders, avoid stockouts, and improve order fulfilment. It helps to forecast demand so businesses can manage seasonal and promotional sales better.
3. Pegging in Automotive Supply Chains
The automotive industry uses pegging to match parts inventory to production to ensure on-time vehicle assembly and efficient use of resources. By linking demand for specific components to available supply, manufacturers can avoid production delays and reduce inventory costs.
Challenges and Limitations of Pegging
Despite the benefits, pegging comes with technical and operational challenges that businesses need to overcome. Here are some of the common ones:
1. Complexity in Large Supply Chains
Big operations with multiple suppliers and production facilities need advanced ERP systems to manage pegging. Without proper coordination, pegging can get overwhelming and cause delays and misallocation of resources.
2. Technology and Software Requirements
Pegging requires MRP and ERP software, which can be expensive to implement and requires extensive employee training. Companies without modern digital infrastructure may struggle to adopt and maintain pegging systems.
3. Data Accuracy and Maintenance
If supply chain data is incomplete or outdated, pegging can lead to wrong supply allocation and inventory shortages. Regular data audits and automated tracking systems are needed to ensure accuracy and prevent errors.
Conclusion
Pegging is a game-changer in supply chain management, giving you unmatched visibility, efficiency, and responsiveness. Whether in manufacturing, retail, or automotive, pegging makes for better decisions, lower costs, and higher customer satisfaction.
Think of pegging as a GPS for your supply chain—without it, you’re flying blind, but with it, every resource is allocated with precision. As industries evolve and digital transformation accelerates, pegging will become even more critical for businesses that want to stay in the game.
If your supply chain is still based on guesswork and old inventory tracking, it’s time to get pegging and transform the way you manage demand and supply.