What Is Co-Manufacturing, Co-Packer, and Co-Man?
What is co-manufacturing, co-packer, and co-man? Learn the differences, benefits, industries, and when to choose each for production, packaging, and business growth.
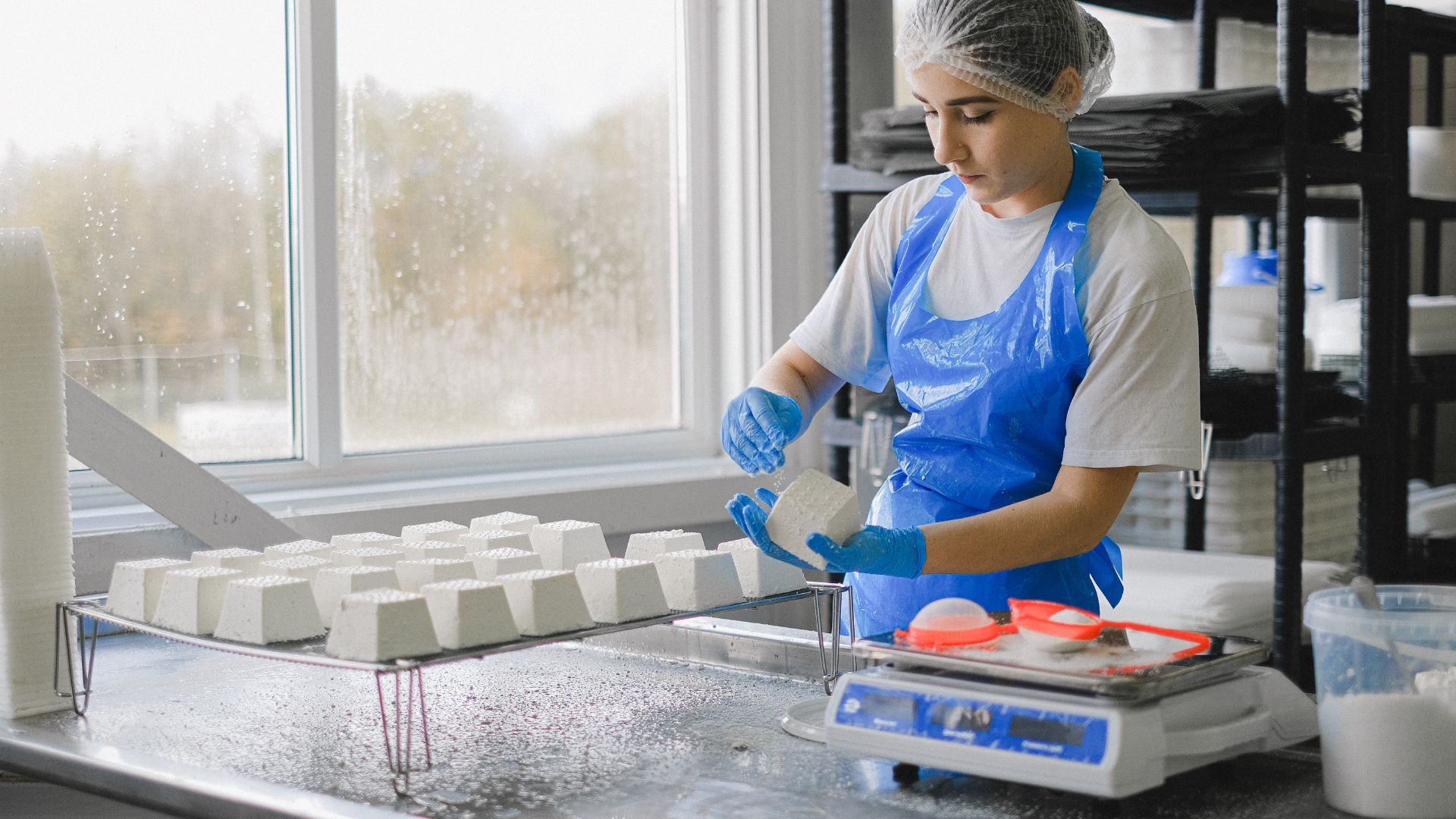
200+ buyers trust Torg for sourcing
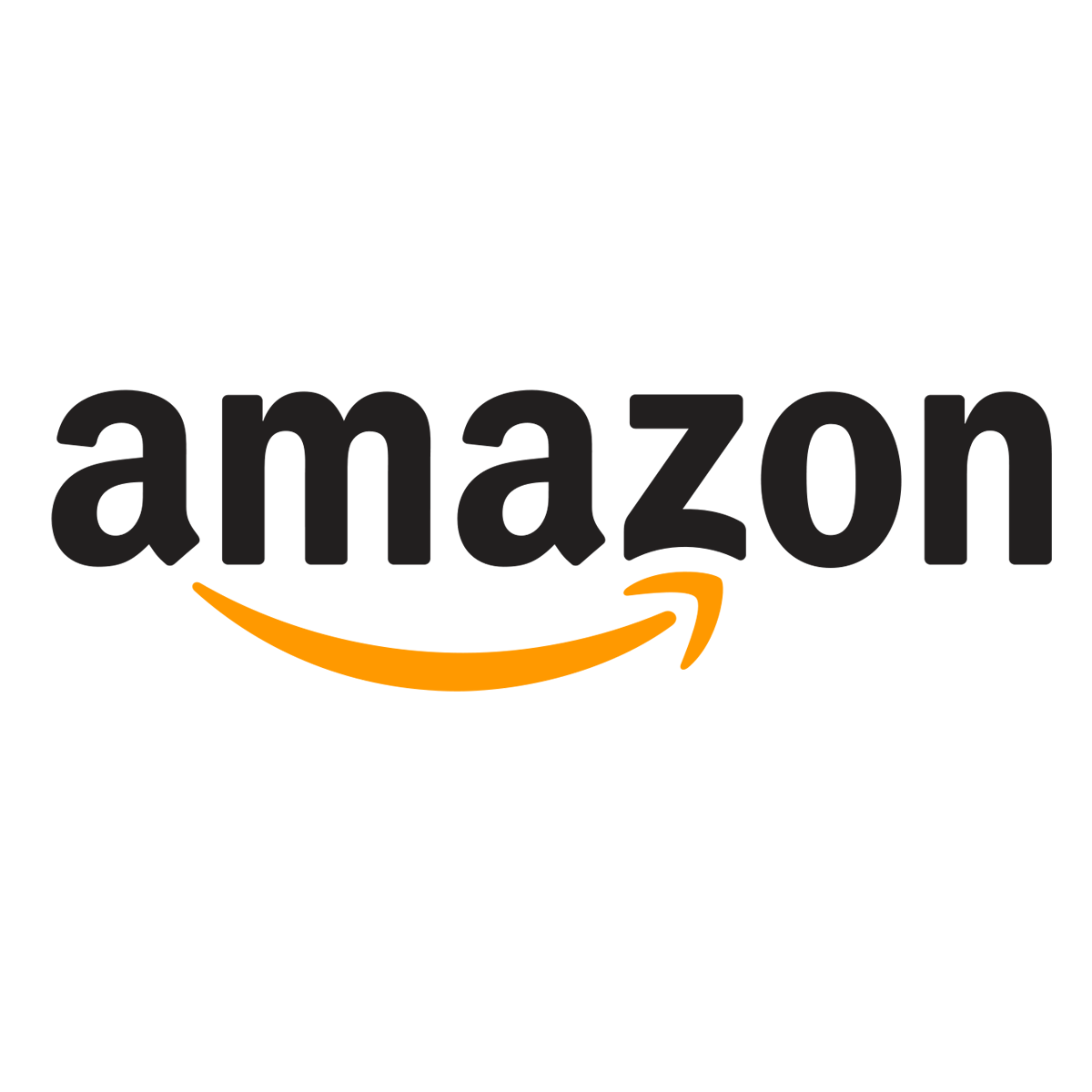
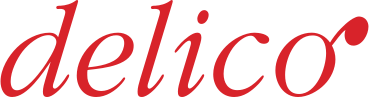
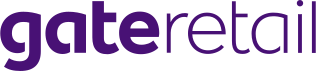
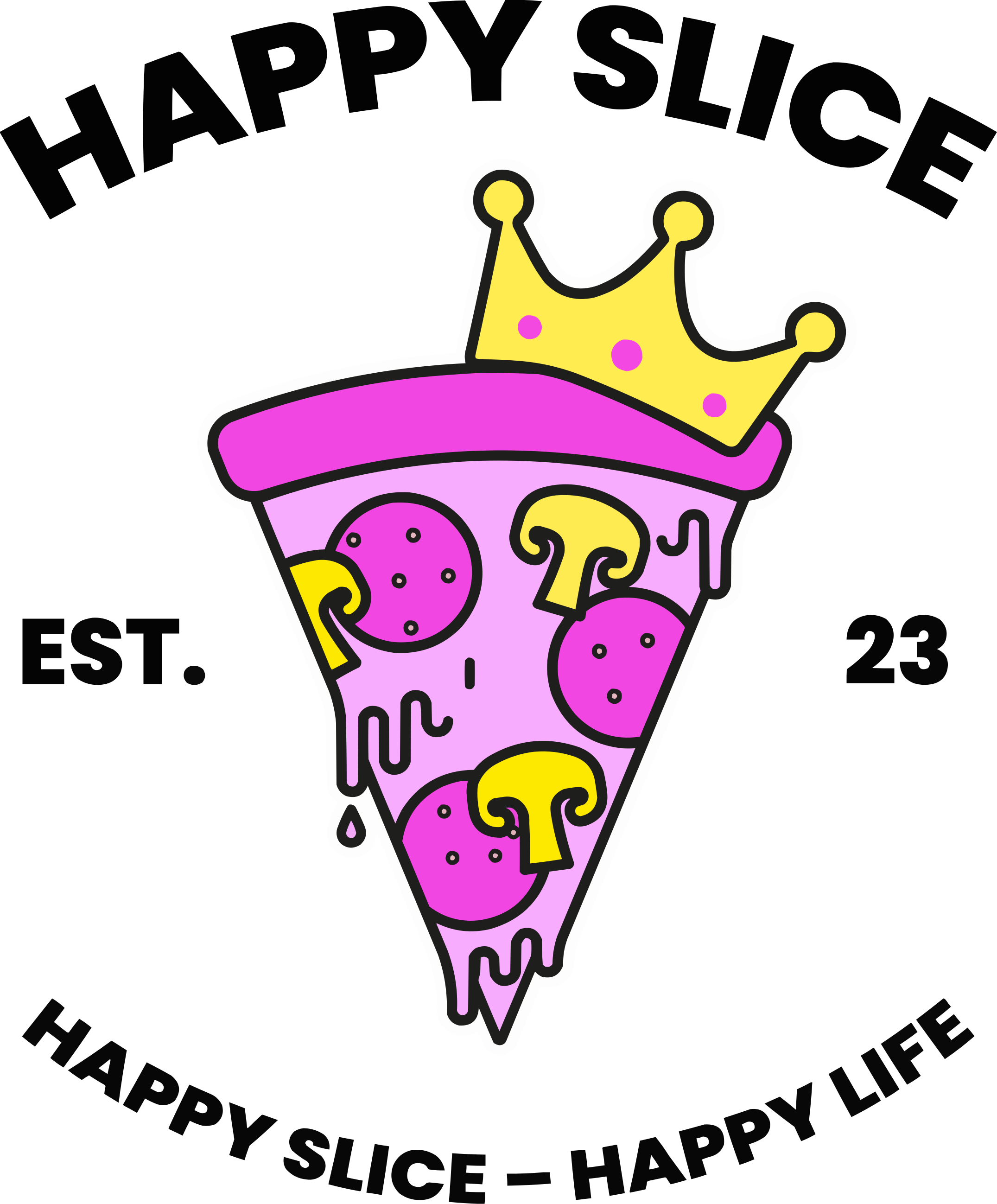
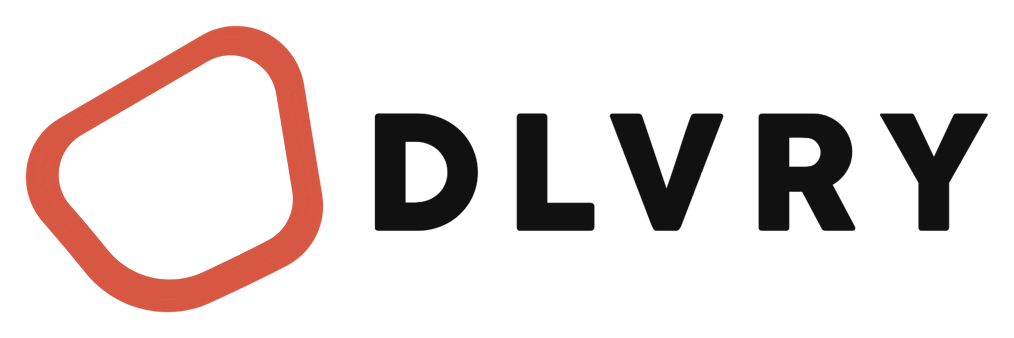
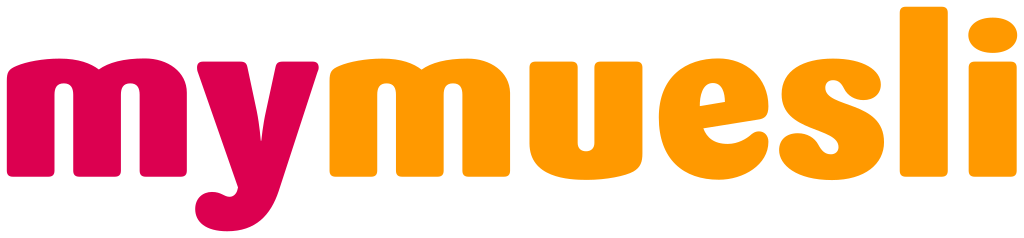
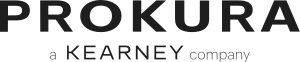
How do big brands make thousands—if not millions—of products without having ginormous factories? That's the magic of co-manufacturing and co-packing. These are terms commonly used to refer to outsourcing manufacturing and packaging processes in industries such as food, beverage, cosmetic, and pharmaceutical. To businesses, learning about these can be a matter of having an efficient supply chain versus a logistics disaster.
Whether you are a startup that needs to ramp up production or an existing company that wishes to increase your product lines, understanding the functions of co-manufacturers and co-packers can assist you in making better business decisions. Let's break it all down.
What is Co-Manufacturing?
Co-manufacturing is the act of one company teaming up with a third-party manufacturing firm to have them make their products on their behalf. It is different from regular manufacturing where a firm has its own premises and facilities; co-manufacturers (or "co-mans") deliver the production ability, workforce, and expertise to make products under a client's requirements.
Differences Between Co-Manufacturing and Traditional Manufacturing
- Ownership of Facilities – The traditional manufacturers own and manage their factories, incurring all the investments in equipment, labor, and maintenance. Co-manufacturers, however, are independent and produce for multiple customers, distributing costs over different brands and minimizing the financial burden on one business.
- Flexibility – Businesses using co-manufacturers can scale production up or down based on demand without being locked into long-term facility investments. This is especially beneficial for seasonal products or brands testing new markets.
- Expertise and Compliance – Co-manufacturers specialize in particular manufacturing methods and regulatory requirements of industries. You receive high-quality manufacture, sophisticated technology and inherent compliance without large upfront capital outlay. Particularly applicable in highly regulated sectors such as pharmaceuticals and food.
Benefits of Co-Manufacturing for Companies
Companies consider co-manufacturing because of the following advantages:
- Less Capital Requirements: In co-manufacturing, companies don’t have to incur costs for equipment, maintenance of the production facility and infrastructure. They can use the co-manufacturer’s existing equipment, workforce, and systems. This means they have more funds for other areas of the business such as marketing, R&D, and distribution channel expansion.
- Faster Time to Market: Co-manufacturers already have the equipment, workforce, and systems in place so companies can go from product development to full scale production much faster. This is a huge advantage for brands looking to jump on trends or meet growing demand without delays.
- Scalability: With a co-manufacturer, companies can scale up or down depending on market demand, seasonal trends, or unexpected changes without being stuck with high fixed costs. This prevents overproduction and excess inventory which can be a huge financial burden.
- Compliance: Many co-manufacturers specialize in specific industries and already meet the necessary safety and quality regulations, so brands don’t have to navigate complex compliance requirements. Whether it’s FDA for pharma, USDA for food, or GMP for cosmetics, working with a co-manufacturer makes it easier to stay compliant.
How Co-Manufacturing Works
Co-manufacturing is a partnership where a company (the brand owner) works with a third-party manufacturer to produce products. The co-manufacturer handles production, quality control, and often packaging, while the brand owner focuses on product design, marketing, and distribution. The two parties typically sign a contract outlining responsibilities, pricing, and timelines.
This model allows companies to scale production without investing in their own manufacturing facilities, access specialized expertise, and reduce costs. However, it also involves challenges like reduced control over production and reliance on the co-manufacturer’s performance.
What Is a Co-Packer?
A co-packer, short for contract packer, is a company that specializes in the packaging of products on behalf of another company. In a co-packing arrangement, the co-packer takes already-manufactured products and packages them according to the specifications provided by the brand.
This includes tasks such as filling, labeling, sealing, and boxing the product to prepare it for sale and distribution. Co-packers may handle a variety of packaging needs, from bulk to retail-ready packaging, and they often provide services such as labeling compliance, quality checks, and logistics support.
Benefits of Co-Packing Services
- Cost Savings: Outsourcing packaging to a co-packer eliminates the need for expensive equipment, specialized staff, and facility space. Instead of investing in an in-house packaging line, brands can use a co-packer’s existing setup, cutting costs and freeing up resources for product development and marketing.
- Customization and Flexibility: Co-packers offer a wide range of packaging options—bottles, pouches, blister packs, and more—giving brands the flexibility to switch formats based on market trends. Whether it’s launching a limited-edition package or changing sizes to meet retailer demands, co-packers make it easy to adapt without major investments.
- Compliance and Efficiency: Regulatory standards for packaging can be complex, especially in industries like food, cosmetics, and pharmaceuticals. Co-packers are already set up to meet these requirements, ensuring products are correctly labeled, sealed, and packaged to avoid compliance issues. Their streamlined processes also minimize waste and reduce packaging errors, keeping production smooth and cost-effective.
What Is a Co-Man?
A "co-man" typically refers to a co-manufacturer, which is a company or business that partners with another company to help manufacture its products. This arrangement allows businesses to outsource their production to a specialized manufacturer that has the necessary expertise, equipment, and facilities.
In the context of the food industry, for example, co-manufacturers might work with a brand to produce their food products, while the brand focuses on marketing, sales, and product development.
Co-Manufacturing vs. Co-Packing: Key Differences
Scope of Work
Co-manufacturing covers the full production process, including formulation, production, and quality control. The co-manufacturer is responsible for turning raw materials into a finished product. Co-packing, however, only deals with packaging the product, such as labeling, boxing, and preparing it for sale, without altering the actual product.
Ownership of Product
In both co-manufacturing and co-packing, the brand retains ownership of the product. However, in co-manufacturing, the co-manufacturer handles the production, while in co-packing, the co-packer is only responsible for the packaging.
Expertise Involved
Co-manufacturers provide specialized production knowledge and manage the entire manufacturing process, often handling complex production tasks. Co-packers, on the other hand, specialize in packaging and focus on efficient and compliant packaging practices, without being involved in the actual manufacturing of the product.
Typical Industries
Co-manufacturing is common in industries like food and beverage, cosmetics, and pharmaceuticals, where full-scale production is needed. Co-packing is often seen in sectors like food and health supplements, where the product is already made and only needs to be packaged for market distribution.
Time and Investment
Co-manufacturing typically requires a larger upfront investment and long-term planning due to the complexity of production. Co-packing, on the other hand, is more cost-effective and flexible, as it focuses only on packaging and does not involve manufacturing the product itself.
Choosing Between Co-Manufacturing and Co-Packing
Here’s a simple breakdown of when to choose each option:
Choose Co-Manufacturing if:
- You need help producing a new product or scaling production.
- You don’t have the resources or capacity to manage large-scale manufacturing in-house.
- You need assistance with raw materials, production processes, and possibly R&D.
- You are launching a product that requires specialized manufacturing techniques.
- You want to ensure regulatory compliance without building an in-house quality control system.
- You’re looking for long-term manufacturing support to grow your brand consistently.
Choose Co-Packing if:
- Your product is already manufactured, and you only need help with packaging and distribution.
- You need packaging assistance for existing products, including filling, labeling, and sealing.
- You want to maintain control over production but need a third-party expert for packaging.
- You require customized packaging options for different retail channels or product variations.
- You want to reduce packaging costs without investing in your own equipment.
- You need faster turnaround times for seasonal promotions or product launches.
Co-Manufacturing and Co-Packing Case Studies
Co-Manufacturing in the Food Industry
A fast-growing snack brand wanted to expand but lacked the facilities for large-scale production. By partnering with a co-manufacturer specializing in health foods, they ramped up production without major upfront investments. This allowed them to enter new markets quickly, increasing sales by 60% in one year (Food Manufacturing Weekly, 2023).
Co-Packing in the Beverage Industry
A startup beverage company needed flexible packaging options for different retail channels. Instead of investing in their own packaging line, they worked with a co-packer who provided multiple formats, from cans to bottles. This helped them meet retailer demands without high costs, leading to a 30% increase in distribution (Beverage Industry Report, 2023).
Co-Manufacturing and Co-Packing in Cosmetics
A skincare brand outsourced both manufacturing and packaging to scale up production while maintaining strict regulatory compliance. Their co-manufacturer produced the formulas, while a co-packer handled packaging for different product sizes. This streamlined their supply chain and helped them launch five new products in under a year (Cosmetic Business Insights, 2023).
Conclusion
Outsourcing through co-manufacturing or co-packing can give businesses a competitive edge, whether by cutting costs, improving efficiency, or scaling production without heavy investments. Co-manufacturers take care of end-to-end production, while co-packers focus on packaging and distribution—each serving a different but crucial role in the supply chain. Choosing the right partner depends on your needs: Do you need full production support or just packaging expertise?
Knowing the difference helps businesses avoid unnecessary costs, streamline operations, and bring products to market faster. Whether you're scaling up or refining your operations, the right co-manufacturer or co-packer can help you increase efficiency, reduce costs, and stay competitive.